As a key device for obtaining information, MEMS sensors play a huge role in promoting the miniaturization of various sensing devices, and have been widely used in space satellites, launch vehicles, aerospace equipment, aircraft, various vehicles, biomedical and consumer electronics.
With the development of electronic technology, the application fields of MEMS are becoming more and more extensive, moving from the earliest industrial and military aviation applications to ordinary civilian and consumer markets. On smart phones, MEMS sensors provide a wide range of applications in sound performance, scene switching, gesture recognition, orientation, and temperature/pressure/humidity sensors; In cars, MEMS sensors enhance vehicle performance through the use of airbag collision sensors, tire pressure monitoring systems (TPMS), and vehicle stability control; In the medical field, micro insulin injection pumps have been successfully developed through MEMS sensors, making heart bypass grafting and artificial cell tissue practical treatment methods in reality; In wearable applications, MEMS sensors can achieve motion tracking, heart rate measurement, and more.
Currently, pressure sensors, accelerometers, gyroscopes, and flow sensors collectively account for 99% of automotive MEMS systems.
MEMS pressure sensors are the most widely used sensors in automobiles, with at least 18 automotive application areas promoting the growth of pressure sensors, including tire pressure, brake sensors in electronic stability control systems, side airbags, engine control related to increasingly strict emission standards, atmospheric pressure, and exhaust gas recirculation pressure. This sensor uses monocrystalline silicon as the material and uses MEMS technology to create a force sensitive membrane in the middle of the material. Then, impurities are diffused on the membrane to form four strain resistors, which are connected into a circuit using a Wheatstone bridge to achieve high sensitivity. There are several common forms of MEMS pressure sensors for vehicles, including capacitive, piezoresistive, differential transformer, and surface acoustic wave.
MEMS accelerometer The principle of MEMS accelerometer is based on Newton's classical mechanics law. It is usually composed of a suspension system and a detection mass. Acceleration detection is achieved through the offset of micro silicon mass blocks. It is mainly used for automobile airbag systems, anti-skid systems, automobile navigation systems, anti-theft systems, etc. In addition to capacitive and piezoresistive types, MEMS accelerometers also have piezoelectric, tunnel current Resonant type and thermocouple type. Among them, capacitive MEMS accelerometers have the characteristics of high sensitivity and minimal temperature influence, making them the mainstream product in MEMS micro accelerometers.
Micro gyroscope is an angular rate sensor mainly used for GPS signal compensation in automotive navigation and automotive chassis control systems, mainly consisting of vibration type, rotor type, and other types. The most widely used type belongs to vibration gyroscopes, which use the Coriolis effect generated by the vibrating mass blocks of monocrystalline or polycrystalline silicon when rotated by the base to sense angular velocity. For example, when a car is turning, the system measures the angular velocity through a gyroscope to indicate whether the steering wheel is in place. It actively applies appropriate brakes on the inner or outer wheels to prevent the car from leaving the lane. Typically, it forms an active control system together with a low accelerometer.
MEMS flow sensor MEMS flow sensor is based on the principle of traditional hot film anemometers and utilizes advanced thin film technology to process stable thin film resistors onto a single thin film. Due to the use of MEMS processing, on the one hand, the sensor response time is shortened, and on the other hand, the front and rear bridge circuits are used to determine the flow direction of the fluid and further measure the reflux flow rate. In order to prevent the impact of temperature changes on measurement accuracy, two thermistors are used in the sensor to compensate for the temperature of the front and rear bridges. The flow sensor is mainly used to detect the air intake and fuel injection volume of the engine, thereby controlling the air fuel ratio near the optimal value. In addition, the flow sensor is widely used in many aspects such as exhaust gas recirculation, anti slip drive, brake anti lock system, and electronic control suspension.
According to sales, the top five automotive MEMS applications ranked in descending order are ESC, airbags, intake manifold absolute pressure (MAP), TPMS, and roll detection.
The application of consumer electronics MEMS sensors has emerged with the rapid development of the consumer electronics field and product innovation, especially benefiting from the rapid development of smartphones and tablet panels. Consumer electronics has replaced the automotive field as the largest application market for MEMS. MEMS sensors in mobile phones and tablets account for almost 90% of the consumer electronics MEMS sensor market. The applications of MEMS sensors in the field of consumer electronics include motion/fall detection, navigation data compensation, gaming/human-machine interface, power management, GPS enhancement/blind spot elimination, speed/distance counting, etc. These MEMS technologies have greatly improved the user experience.
The fall protection of hard drives in terminal devices is one of the representative applications of MEMS motion sensors with significant historical significance in the consumer electronics market. The three-axis accelerometer inside the laptop can monitor acceleration because it has specific functions and data processing circuits. It can detect unexpected falls of the hard drive and promptly command the read and write head to retract to a safe position to prevent damage to the read and write head when the computer eventually falls on the floor.
Mobile phones are the largest application area of MEMS in consumer products. Including MEMS microphones, 3D accelerators, RF passive and active components, gyroscopes for camera stabilization and GPS, small fuel cells, and biochemical chips, the most commonly used sensors are accelerometers, gyroscopes, and MEMS silicon microphones, with accelerometers being the largest application product in this market. Recently, gyroscopes have grown rapidly and have become the second largest application product after accelerometers.
The sales of MEMS microphones have exceeded $1 billion in 2015, and the IHS Global Industry Research Report in the United States states that the global MEMS microphone market will continue to maintain a compound annual growth rate (CAGR) of 18% for five consecutive years. There are also some MEMS sensors that have just entered the market, such as magnetometers, fingerprint sensors, environmental sensors, MEMS mobile cameras, etc. The number, scale, and diversity of MEMS sensors in mobile applications are still growing rapidly.
Apple first applied MEMS accelerometers to the iPhone in 2007, ushering in a sensor revolution in the mobile phone industry. The iPhone 6 Plus uses MEMS sensors such as accelerometers, gyroscopes, electronic compasses, barometers, fingerprint sensors, proximity and ambient light sensors, MEMS microphones, and Image Sensors. So far, Apple has owned over 350 invention patents related to sensors, including applications for touch control, imaging, motion, vibration sensing, data processing, drop perception, and brightness perception.
The game console is a prominent representative of motion tracking and gesture recognition applications. Taking the revolutionary Nintendo Wii game console as an example, it uses MEMS three-axis accelerometer to capture any minute action of the player, so that the player can be intoxicated with the real game experience and integrated into the game through different actions, such as imitating a real tennis game, an attractive golf game The act of a tense boxing or relaxed fishing match.
High energy efficiency and low cost micro MEMS sensors have completely changed the way people interact with mobile terminal devices. On various mobile terminals, game consoles, remote controls, and other devices, MEMS sensors can achieve advanced functions and exciting user interfaces. Users can activate corresponding functions with their gestures and touch. It marks a milestone footnote for the "upgrading and upgrading" of consumer electronics. Intelligent wearable devices are currently the most popular emerging product, and the sensing components used in them typically face stricter requirements in terms of size, power consumption, sensing sensitivity, or component reliability. The most successful component cases are inertial sensors and MEMS microphones, including well-known manufacturers such as Google, Apple, Microsoft, and Motorola, which have integrated these two components into their own wearable device products and become their standard sensor equipment.
The two major functional projects of intelligent wearable devices are quantitative self and portable environmental safety monitoring. The required sensing functions can roughly include four categories: activity sensing, image sensing, environmental sensing, and physiological sensing. The application demand of MEMS components in wearable devices is to achieve the goals of miniaturization, low power consumption, high performance, and multi-functional integration of the system.
Fitness and health monitoring are representative applications of MEMS sensors in intelligent wearable devices. A step meter or pedometer utilizes a three-axis MEMS acceleration sensor. In specific situations, the pedometer sensor can accurately measure the acceleration acting on the system during walking and running. By processing acceleration data, the pedometer displays the number of steps and speed taken by the user, as well as the amount of heat consumed during body movement.
Application of MEMS sensors in aerospace equipment
The application of MEMS sensors in the aerospace field requires adaptation to different space environments, including vacuum, electromagnetic radiation, high-energy particle radiation, plasma, micro meteoroid, planetary atmosphere, magnetic field and gravitational field, as well as the induced environment generated when some spacecraft systems are working or under the action of space environment, such as the vibration and impact environment caused by the ignition of orbital control Thruster and the extension of solar cell wings; The induced magnetic field generated by the movement of magnetic materials and current circuits on spacecraft in a spatial magnetic field; Molecular pollution caused by the deposition of organic material emissions on other parts of spacecraft.
Therefore, aerospace sensors mainly include status sensors and environmental sensors. The former includes real-time position sensors of various moving parts, such as flaps, aileron positions, nozzle sizes, throttle positions, speed brake positions, landing gear retraction and retraction positions, aircraft status sensors, such as angle of attack, sideslip angle sensors, aircraft attitude sensors, and various parameters, such as hydraulic pressure, oil pressure, engine vibration, lubricating oil metal chips, Various consumables such as residual fuel, consumption rate, etc., as well as ice sensors, fire alarm sensors, limit sensors, overload sensors, life sensors, and automatic conversion sensors for various excess systems. Environmental sensors mainly include temperature sensors, humidity sensors, oxygen sensors, pressure sensors, flow sensors, etc.
MEMS sensors have five main uses in the aerospace field:
① Provide information about the operation of spacecraft and play a role in fault diagnosis;
② Determine the coordination of work between various subsystems and verify the design plan;
③ Provide the information required for system wide self inspection to provide a basis for commanders' decision-making;
④ Provide internal testing parameters for each subsystem and the entire machine to verify the correctness of the design.
⑤ Monitor the internal and external environment of the aircraft, provide necessary survival conditions for pilots and astronauts, and ensure normal flight parameters.
Electronic devices composed of MEMS sensors
MEMS sensors have important applications in electronic equipment, aircraft design, and micro satellite technologies in aircraft. The airborne distributed air data computer is directly composed of a multi-functional micro atmospheric data probe (or combined pitot tube), a micro pressure sensor (static pressure, differential pressure and dynamic pressure) and a signal processing unit that integrates total pressure, static pressure and angle of attack, and is packaged in the shell to form a MEMS.
MEMS inertial navigation system
The micro inertial navigation system integrates micro gyroscopes, micro accelerometers, and their signal processing units. The system is mainly made of silicon material and manufactured using MEMS processing technology. Its volume and mass are reduced by at least 2-3 orders of magnitude compared to conventional inertial navigation systems.
The micro inertial measurement unit (MIMU) manufactured by MEMS technology has no rotating parts and is greatly superior to conventional inertial instruments in terms of life, reliability, cost, volume and mass. The standardized and high-performance spacecraft attitude measurement instruments produced have better performance, cheaper prices, and can be used on aerospace platforms. The use of MIMU devices can greatly reduce the weight of the device.
MEMS acceleration sensors are used in aerospace applications in attitude and heading reference systems; Strapdown inertial measurement unit; Aircraft navigation system; Flight control system; Structural testing during flight, including flutter testing; Health system testing; Stability testing; Ground vibration test (wind tunnel test); Modal testing; Engine control system, guidance system, etc.
MEMS chemical sensors, a high-temperature sensor array similar to electronic noses, are used to detect and control emissions from aviation and automotive engines. Determine the composition of exhaust gas in the emission system by analyzing the signals generated by the electronic nose.
MEMS pressure sensors are widely used in flight, flight tests, engine testing, structural strength testing, wind tunnel testing, and equipment manufacturing and production processes. The characteristics of pressure measurement are:; There are many types of pressure to be measured, covering a wide range, and multiple pressure measuring points, requiring high measurement accuracy. Aerospace integrates contemporary advanced manufacturing technology, information technology, and material technology, with increasing requirements for sensors. The development direction of MEMS sensors is multifunctional, miniaturized, intelligent, and integrated. With the further improvement of product reliability and price reduction, and the continuous maturity and improvement of manufacturing technology development, the application of MEMS sensors in the aerospace field will replace traditional sensors on a wider range.
The application of MEMS Sensors in the Biomedical Industry
The breakthrough in MEMS sensor technology has also brought unprecedented convenience and experience to medical applications. With the aging population, people's healthcare issues have become unprecedentedly important. People's healthcare issues have become unprecedentedly important. The fields of in vitro diagnosis, drug research, patient monitoring, drug delivery methods, and implantable medical devices are constantly developing, and system integrators need innovative technologies to quickly improve product performance, reduce product costs, and reduce product size.
BioMEMS technology has brought improved sensing and execution functions to all these fields with micro devices, such as acceleration sensors, pressure sensors, flow sensors, and micropumps. The application of pressure sensors in medicine is called medical pressure sensors, and they must be highly accurate and compact in packaging to facilitate portability, especially when the instrument needs to be directly connected to the patient.
Small pressure sensors are now being applied to areas prone to human error, such as infusion pumps for drug administration. This sensor can accurately measure the weight of the infusion bag. When the liquid weight is different from the preset value, the sensor will immediately issue a warning message to the connected device and communicate with the controller in a timely manner.
The core component of a pressure sensor is a foil strain gauge, which uses vacuum deposition or sputtering technology to adhere to the dielectric layer through molecular bonding of the material. This technology is commonly referred to as the thin film method. The ideal strain gauge should be small in size, low in cost, extremely sensitive to strain in the direction of load, and not affected by changes in ambient temperature.
Implantable sensors should be small in size, light in weight, and compatible with the body, while also requiring very low power. More importantly, they cannot decay over time.
As these sensors belong to Class III medical devices, they require approval from the Food and Drug Administration (FDA) to be used. Generally speaking, these types of sensors are very expensive and require expert surgery for transplantation. The requirement for power is one of the main challenges faced by implantable sensors for normal operation. Sensors that can function without power are the most perfect. Piezoelectric polymer sensors have small size, high reliability, no need for external power, and can work continuously for a long time. This type of sensor can be applied to a pacemaker that monitors patient activity, and implantable sensors can monitor heart rate changes in real-time. For example, due to a large aneurysm growing in the abdomen, it is required to remove a portion of the fragile artery and replace it with an artificially synthesized tubular organ. At this point, a sensor can be implanted during the surgery to monitor the pressure leakage at the surgical site.
The pacemaker generates a signal from the sensor whenever the patient is exercising. The pacemaker receives these signals and causes the heart to pulsate accordingly. If the patient is resting and the signal is zero, the pacemaker will cause the heart to beat at a normal frequency, such as approximately 70 beats per minute. Sensors can distinguish various activities, such as walking, running, or other physical activities. The output of the sensor is proportional to the amount of motion.
MEMS acceleration sensor proposes a non-invasive fetal heart detection method, and develops a simple, intuitive and accurate medical auxiliary instrument between the fetal heart stethoscope and Doppler fetal monitor for clinical diagnosis and maternal self inspection.
The fetal heart rate is converted into an analog voltage signal through an acceleration sensor, and the difference amplification is achieved through an instrument amplifier used for pre amplification. Then perform a series of intermediate signal processing such as filtering, and use an A/D converter to convert the analog voltage signal into a digital signal. Input the optical isolation device to the microcontroller for analysis and processing, and finally output the processing results.
The fetal heart rate detector designed based on MEMS acceleration sensors can be used as a remote fetal heart rate monitoring system with appropriate improvements. The central signal collection, analysis, and monitoring host on the hospital end provides automatic analysis results, and doctors diagnose the results. If there are any problems, pregnant women should be notified to come to the hospital in a timely manner. This technology is beneficial for pregnant women to check the condition of the fetus at any time, ensuring the health of the fetus and pregnant women.
A biosensor is sensitive to biological substances and converts their concentration into electrical signals for detection. It is an analytical tool composed of immobilized biological sensitive materials as recognition elements (including enzymes, antibodies, antigens, microorganisms, cells, tissues, nucleic acids, and other bioactive substances), appropriate physical and chemical transducers (such as oxygen electrodes, photosensitive tubes, field-effect transistors, piezoelectric crystals, etc.), and signal amplification devices. In clinical medicine, enzyme electrodes are the earliest developed and most widely used sensor. Microbial sensors can be made by replacing enzymes with microorganisms with different biological characteristics. Biosensors have been applied to monitor various bacteria, viruses, and their toxins. The typical representative product of biosensors for drug analysis is SPR biosensor, which is a kind of surface facial mask resonance analysis and a technology for real-time determination of biomolecular binding.
The most common applications for biosensing include antibody antigen interactions, nucleic acid interactions, enzyme interactions, cell interactions, and interactions using biomimetic materials.
With the development of medical technology, more and more healthcare applications are using MEMS devices, which has led to strong market growth! MEMS sensors help the Internet of Things build a better life in an intelligent world. Everything is connected and intelligently sensed. With the rapid development of communication technology, the application of MEMS sensor technology enables all intelligent objects to interact with the real world, driving the development of the Internet of Things.
The Internet of Things (IoT) is a network that connects any item to the Internet for information exchange and communication, in order to achieve intelligent identification, positioning, tracking, monitoring, and management. In short, the Internet of Things is the "Internet of Things Connected".
From the perspective of network structure, the Internet of Things can be divided into perception layer, network layer, and application layer. The perception layer is located at the bottom of the three-layer structure of the Internet of Things and is the core foundation of the Internet of Things. Sensors, as an important component of the perception layer of one of the three hierarchical structures of the Internet of Things, convert physical, chemical, and biological quantities in the real world into digital signals that can be processed, which is the foundation and prerequisite for achieving the Internet of Things.
The vigorous promotion of the Internet of Things and the widespread application of intelligent terminals have led to a significant increase in demand for sensor products, and the focus has gradually shifted to the field of MEMS sensors with higher technological content. MEMS technology is widely used in the field of the Internet of Things, covering multiple sub fields such as wearable devices, smart homes, healthcare, Industry 4.0, smart cars, and smart cities.
Human beings engage in comprehensive community communication and information sharing through a massive intelligent network infrastructure shared by hundreds of millions of people worldwide, and achieve ubiquitous detection, identification, control, and services through the integration of linked physical objects and virtual analysis.
In the future world of infinite sensing and interconnected everything, there are various intelligent technologies: unmanned vehicles will automatically drive, making driving safer; Smart home appliances provide convenient and comfortable housekeeping and security services; Plant factories accurately grasp the crop production process and solve the food shortage problem caused by climate change; Industry 4.0 achieves safe and efficient human-machine collaboration, improves product yield and quality; The long-distance medical network brings higher quality and convenient medical services; Smart grids enhance urban energy efficiency, drive economic growth, and mitigate the global greenhouse effect. For individuals, mobile and wearable devices will provide ubiquitous information services and daily care. In addition, traditional industrial applications, such as medical, navigation, military, aviation, seismic exploration and process control, use MEMS sensing component technology to form a new type of industrial internet of things.
The sensors of MEMS technology are precisely characterized by low power consumption, high accuracy, and small size to meet the intelligent world of interconnected everything. The development, design, and market investment of new MEMS sensors make it possible to have more diverse and colorful IoT applications, which promotes our lives to be more colorful.
Ericco offers a variety of high-precision MEMS gyroscopes. If you would like more technical data and quotations, please feel free to contact us at any time.
More Technical Questions
1.How to apply MEMS sensor in Oil & GasᅵAerospaceᅵAHRSᅵUAV?
2.Precision MEMS Sensors Realize New Navigation Applications
3.What is MEMS Sensor and its Technical Advantages?
4.The Development Potential of MEMS Sensors
5.Application of MEMS Sensors in Aerospace Equipment
Products in Article
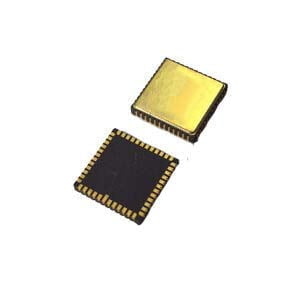
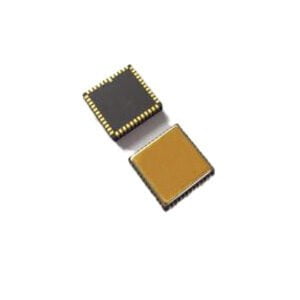
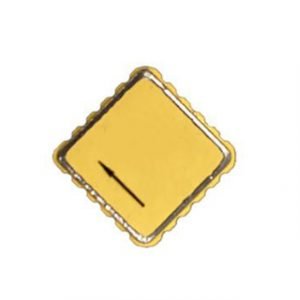
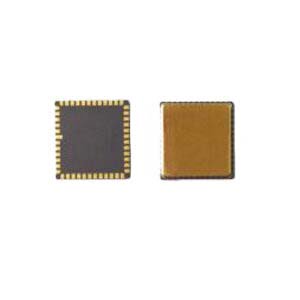
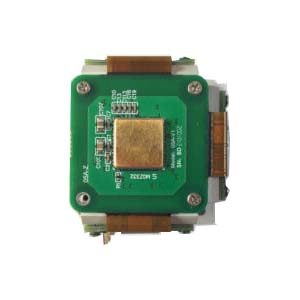
