Piezoresistive sensors are devices that are fabricated by diffusion resistance on a substrate of a semiconductor material in accordance with the piezoresistive effect of the semiconductor material. The substrate can be directly used as a measuring sensor element, and the diffusion resistor is connected in the form of a bridge in the substrate. The sensor uses the integrated technology to integrate the resistance strip on the monocrystalline silicon membrane to make the silicon piezoresistive chip, and the peripheral of the chip is fixed in the shell, and the electrode lead is drawn. Piezoresistive pressure sensor is also called solid state pressure sensor, which is different from the adhesive strain gauge that needs to feel the external force indirectly through the elastic sensitive element, but directly through the silicon diaphragm to feel the measured pressure.
When the substrate is deformed by an external force, the resistance values will change, and the bridge will produce a corresponding unbalanced output. The substrate (or diaphragm) used as a piezoresistive sensor is mainly a silicon wafer and a silicon wafer, and the silicon piezoresistive sensor made of a sensitive material is more and more popular, especially in measuring pressure. And speed solid state piezoresistive sensors are most commonly used.
The working principle diagram of the piezoresistive pressure sensor is as follows:
The working principle of piezoresistive sensors
A strain gage is a sensitive device that converts the strain change on the device under test into an electrical signal. It is one of the main components of a piezoresistive strain sensor. The most widely used resistance strain gauges are metal resistance strain gauges and semiconductor strain gauges.
The working principle of the metal resistance strain gauge is a phenomenon in which the strain resistance adsorbed on the base material changes with the mechanical deformation, which is commonly called the resistance strain effect. When the strain gauge substrate is subjected to stress changes, the strain gauge is deformed, and the resistance of the strain gauge is changed, resulting in a voltage change applied to the resistor. Such strain gauges typically have a small change in resistance when subjected to force. Generally, such strain gauges are formed into strain bridges and amplified by subsequent instrumentation amplifiers, and then transmitted to a processing circuit display or actuator for operation. One step of processing.
Application of piezoresistive sensors
Piezoresistive sensors are widely used in aerospace, aviation, navigation, petrochemical, power machinery, biomedical engineering, meteorology, geology, seismic measurement and other fields. Pressure is a key parameter in the aerospace and aviation industry, which requires high precision in the measurement of static and dynamic pressures, local pressures and the whole pressure field. Piezoresistive sensor is an ideal sensor for this purpose. For example, it is used to measure the airflow pressure distribution of helicopter wings, the dynamic distortion of engine intake, the fluctuating pressure of cascade and the wing jitter. In the measurement of the central pressure of aircraft jet engines, a specially designed silicon pressure sensor is used, and its operating temperature is above 500℃. A silicon pressure sensor with a precision of 0.05% is used in the atmospheric data measurement system of Boeing passenger aircraft. In the scaled down wind tunnel model test, piezoresistive sensors can be densely installed at the wind tunnel inlet and in the engine intake line model.
Piezoresistive sensors are also effectively used in the measurement of explosion pressure and shock wave, vacuum measurement, monitoring and control of the performance of automobile engines, and measurement of weapons such as measuring the pressure in the chamber of a gun and launching shock wave. In addition, piezoresistive sensors are widely used in oil well pressure measurement, direction finding while drilling, fault detection of underground sealed cables, and flow and level measurement. With the further development of microelectronics technology and computers, the application of piezoresistive sensors will develop rapidly.
More Technical Questions
1.Multi-Dimensional Understanding of High Precision Quartz Accelerometer
2.How do parameters affect the performance of the quartz accelerometer?
3.Application of Quartz Accelerometer in UAV and Positioning System
4.How to Distinguish MEMS Accelerometer and MEMS Gyroscope Correctly?
5.Analysis of the main performance parameters of MEMS gyroscope
6.Application of MEMS Accelerometer in North Finder
Products in Article
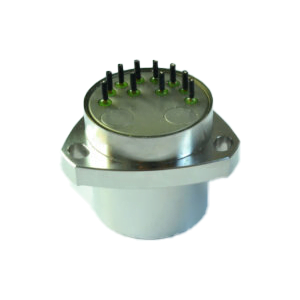
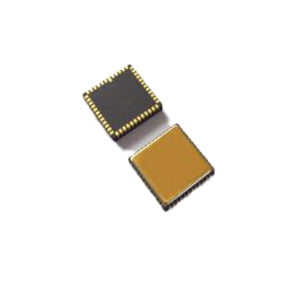
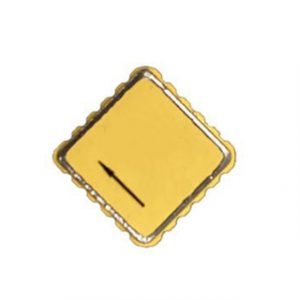
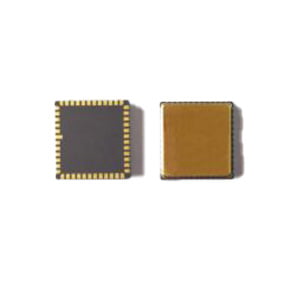
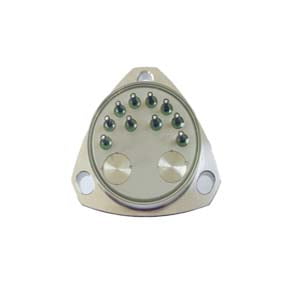
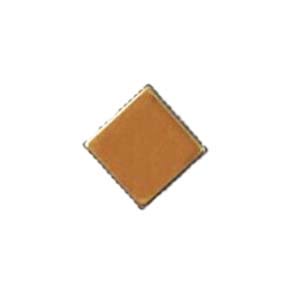