The accuracy of wellbore trajectory positioning is critical to the success of offshore drilling operations, especially in environments with a high risk of wellbore collisions. The use of gyroscopic technology to implement drilling operations can reduce this risk, and gyroscopic measurement technology can improve measurement accuracy, reduce the risk of wellbore collision, and improve the spacing factor between wells.
Over the past decade, the need to minimize non-productive time and make drilling operations more efficient has prompted a wave of new technology releases aimed at drastically reducing the days-to-depth curve. Through continuous innovation, the average time to drill a well has been shortened significantly, resulting in significant technical achievements.
Compared to magnetic surveying MWD (measurement-while-drilling) tools, gyroscopic measurement technology is considered to be a better choice because it can provide more accurate measurement data without worrying about magnetic interference. As oil and gas well designs become more complex, GWD (Gyroscopic Measurement While Drilling) systems continue to expand the use of this technology, enabling real-time measurement data collection while drilling. In addition, the pioneering of solid-state gyroscope technology has led to the introduction of new systems that are stronger, more durable, and more accurate in measurement than previous products.
Offshore oil and gas drilling, because most of them drill multiple wells on one drilling platform, also known as batch drilling, collisions between wells are easy to occur. Once a collision occurs, it may lead to catastrophic HSE (health, safety and environmental protection) incidents. Therefore, continuous innovation and support of measurement technology is required.
gyro technology
GWD technology collects real-time measurement data, which enables more accurate wellbore positioning and safer drilling operations. The GWD system can be used with the most commonly used MWD tools and does not require the use of wired gyroscopes to orient or steer the BHA and drill. When accurate wellbore steering is critical for collision avoidance and trajectory positioning, the use of GWD systems to obtain real-time information on wellbore orientation to improve operational performance and safety may be a major factor different from traditional MWD.
The current all-around solid-state gyroscope, powered by a new set of sensors, has two independent three-axis sensor probes. These solid-state sensor probes accurately measure the Earth's rotation rate and are more robust than conventional designs. The system is immune to mass unbalance errors, requires no post-run calibration, and can collect measurements during order follow-up, reducing unnecessary downtime in oil drilling.
ERICCO's ER-MG2-100 ,a high performance MEMS gyro sensor with 0.01-0.02°/hr bias instability and 0.0025-0.005°/√hr Angular Random Walk, is specially designed for north seeking, pointing, initial alignment in logging tools/gyro tools, mining/drilling equipment, weapon/UAV launch systems, satellite antenna,target tracking system and so on,can be used in GWD to provide real-time azimuth, inclination and tool face measurement data, while the bias instability of ER-MG2-100 is 0.02°/h, which can improve the measurement accuracy, thereby improving the well spacing factor to meet the dual goals of wellbore positioning accuracy and measurement efficiency.The ER-MG2-50/100 is available in a hermetically sealed ceramic LCC surface mount package, and is capable of operating at 5V supply and a wide temperature range (−45°C to +85°C).As an advanced differential sensor design, it suppresses the effects of linear acceleration, enabling the ER-MG2-50/100 to operate in extremely harsh environments where shock and vibration are present.
fiber optic gyroscope manufacturers
how does a mems gyroscope work
fog gyro
fiber optic gyro price
mems gyro
fiber optic gyroscopes
piezoresistive sensor
fiberoptic gyroscope
fiber optic gyro
More Technical Questions
1.Do You Know Fiber Optic Gyroscope and Its Typical Applications?
2.Application of Fiber Optic Gyroscope
3.Principle and Application of Fiber Optic Gyroscope
4.Development of MWD for Directional Drilling
5.What Is The Difference Between MWD And LWD?
6.Possible Problems And Solutions For Shallow Testing Of MWD Instruments
Products in Article
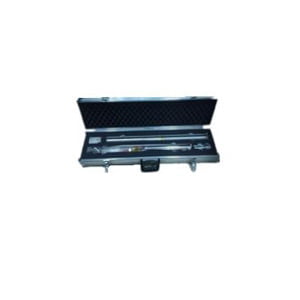
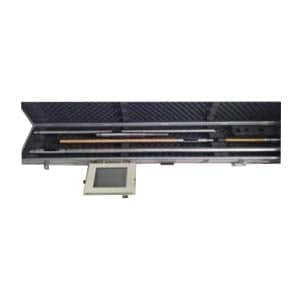
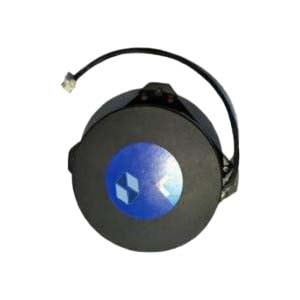
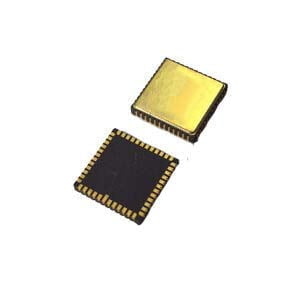
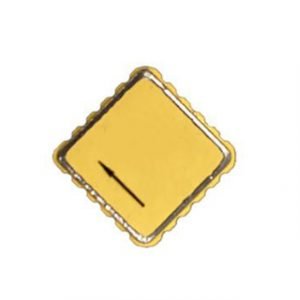
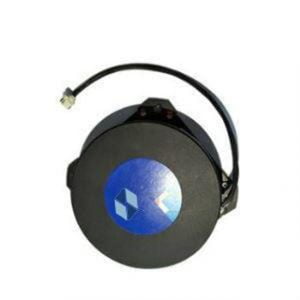