Different definitions:
LWD(Logging While Drilling) generally refers to the measurement of formation petrophysical parameters during drilling, and the data telemetry system is used to send the measurement results to the surface in real time for processing. Due to the limitation of data transmission technology, a large amount of data is stored in the memory of downhole instruments and played back after drilling.
Measurement While Driling (MWD) is an advanced technology in directional drilling, which allows continuous directional drilling to measure certain information near the bottom of the bit hole and immediately transmit the information to the surface.
Small diameter measurement while drilling (MWD-Φ38mm) is designed based on this principle, and has the characteristics of high precision, high stability and high vibration resistance. Rubber wings with different diameters (drill collar diameter of 50.8mm, 71.4mm) can be selected according to the situation of drilling tools on site to adapt to different drilling tools. In the construction of small holes, the hole without magnetic drilling tool can not be reamed (the diameter of the drill collar is 50.8mm), which reduces the erosion of the drill tool and enhances the safety of the downhole drilling tool. It can also be used for conventional large hole construction.
At present, the main technology in horizontal well drilling is MWD (ie, logging while drilling), and the one used for formation evaluation is called LWD (logging while drilling or FEMWD—measurement while drilling system for formation evaluation). The measurement while drilling system is composed of downhole sensor components, data transmission or downhole recording devices and surface detection and processing equipment. All while drilling systems use sensors close to the upper part of the bit to measure drilling parameters and formation parameters. The data measured during drilling is transmitted to the ground in real time. MWD can generally measure well deviation, azimuth and tool face direction. In addition to the above, LWD can also measure resistivity, natural gamma, lithological density, neutron, acoustic wave and other formation parameters.
In addition, drilling tool vibration analysis technology can also be used to guide directional drilling. The key technology of LWD is signal transmission, which is widely used in drilling fluid pressure pulse transmission, which is a common method used by LWD instruments. It converts measured parameters into drilling fluid pressure pulses and transmits them to the surface along with drilling fluid circulation.The basis for successful horizontal well drilling is LWD data and MWD direction data.Its advantage is that the transmission rate is high and it is not affected by the drilling fluid properties. In addition, there are downhole storage methods, all the data is stored in the downhole memory, to be recovered after drilling. The advantages are low cost and reliable data storage. The disadvantage is that the surface can not get real-time data, can not guide drilling. LWD tools provide information that can evaluate the formations drilled in the borehole. These data determine how to change the direction of the borehole to achieve the desired goal. This method is called "geosteering".
Geosteering technology includes reliable steering system (MWD), improved new-type stratum physical measurement, logging data model, near-bit sensor and measurement transmission motor, and detailed structure map with three-dimensional seismic processing. The following are typical bottom hole combinations and drill string combinations used in geosteering drilling: drill bit + geosteering system (measurement motor, near-bit resistivity, gamma and well deviation, launched to the receiving end section) + geo-steering tool acceptance End section (used to receive data from the steering system, LWD logging quality, resistivity and Gamma data) + MWD inclinometer (the heart of measurement, power supply inclinometer and data transmission) + non-magnetic drill collar (for Minimize the azimuth error of MWD or install LWD neutron porosity instrument)+ drill pipe.
If you want to get more details about drilling and logging system ,pls visit https://www.ericcointernational.com/drilling-and-logging-system/
More Technical Questions
1.What Is The Principle Of MWD?
2.Development of MWD for Directional Drilling
3.Three Signal Transmission Methods of MWD Inclinometer While Drilling
4.Possible Problems And Solutions For Shallow Testing Of MWD Instruments
5.Wireless Transmission of MWD and LWD
6.GWD – Gyro-while-drilling Technology Superior to Traditional MWD
Products in Article
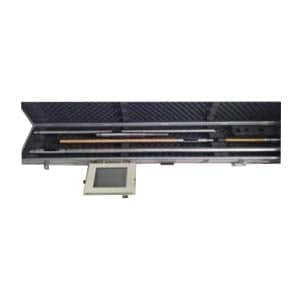
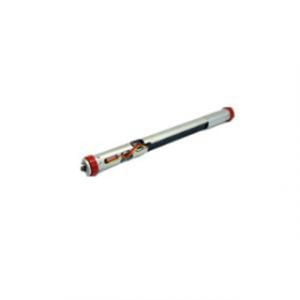
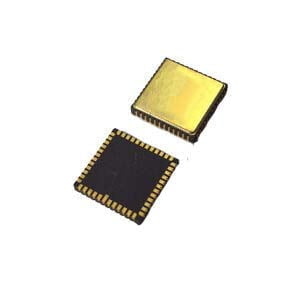
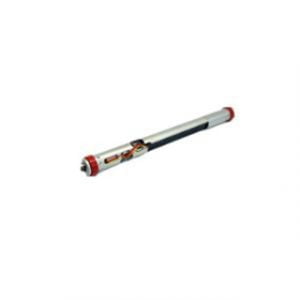
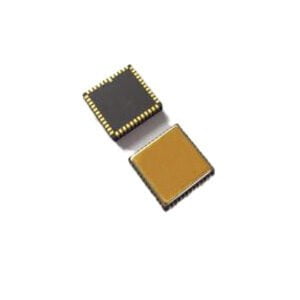
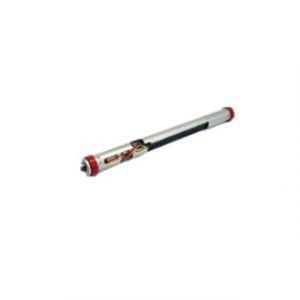