Since its first use in shipborne compasses in 1910, the gyroscope has been more than 100 years old. The process is roughly divided into four stages. The first stage is the ball bearings that support the top of the gyro motor and frame, and the 20th century. The liquid floatation and air float gyro developed from the late 40's to the early 50's; the second phase is the dry power flexible support rotor gyroscope developed since the 1960s; the third phase is represented by the laser gyro and the fiber optic gyro. The optical gyro; currently the development of the gyro has entered the fourth stage, namely the micro-machined gyro.
First generation gyroscope: rotor gyroscope
The ball bearing gyro was first applied to the V-2 missile as the first generation of sub-gyro. Rotor gyroscope is a kind of device that supports a high-speed rotating rigid rotor to obtain rotational degrees of freedom. The key technology of rotor gyroscope lies in the high speed rotation and supporting mode of rotor. The ball bearing gyro uses bearings and ball bearing to support the rotor, because the ball bearing has a large friction torque problem, the drift error is generally in the range of one to fifteen degrees per hour, far from meeting the requirements of the inertial system, has been eliminated.
Second generation gyroscope: liquid float, air float gyro
Liquid float gyroscope is the second generation of rotor gyroscope. Compared with the first generation of ball bearing gyroscope, its main advantage is to use high-density liquid and gas as support instead of mechanical support, so that the internal gyroscope rotor friction is reduced. The so-called liquid floating support means that the float component (two-degree-of-freedom gyro) composed of the rotor and the inner ring is immersed in the float, and the density of the float is large enough to make the buoyancy just balance with the gravity of the float component, so that the load level on the inner ring axis is zero, and the friction torque is small. The static pressure air floating support is to send 2 to 3 atmospheres of gas into the space between the float and the shell to float the gyroscope, and the dynamic pressure air floating support is to use the gas film generated by the high-speed rotation of the rotor to float the rotor.
Third generation gyroscope: flexible gyroscope
The flexible gyro is the third generation rotor gyro. The flexible accelerometer replaces the liquid floating pendulum accelerometer. The gyro rotor is suspended by the flexible support and separated from the driving motor.
The flexible gyro developed rapidly in the 1960s, driven by the navigation needs of aircraft, and was divided into two types, platform and strapdown. The flexible gyro has the advantages of simple structure, low cost, small size and fast start-up. The product yield is low, fatigue and stability problems exist, mechanical error is large, dynamic range is small.
Fourth generation gyroscope:
1. Electrostatic gyroscope: electrostatic gyroscope is the fourth generation rotor gyroscope, which was successfully developed in the 1970s. It uses electrostatic gravity to float the metal ball rotor, which is a more thorough support innovation, high precision, and belongs to the real freedom of the rotor gyroscope.
2.MEMS gyro: nanocrystal gyroscopes (MEMS chips) in MEMS systems are used to detect, measure and interpret changes in angular acceleration and angular velocity. The characteristics of MEMS crystal gyro will oscillate with the change of external angular velocity. The rotor of nanocrystalline gyro in MEMS gyro will produce mechanical vibration with the change of external angular acceleration and angular velocity. The MEMS gyroscope represented by ER-MG2-100 has 0.01-0.02°/hr bias instability and 0.0025-0.005°/√hr Angle random walk. Designed for logging tools/gyro tools, mining/drilling equipment, weapons/UAV launch systems, satellite antennas, target tracking systems, etc., for north finding, pointing, and initial alignment.
3.Laser gyro: refers to the use of laser beam optical path difference measurement object angular displacement device. If the object moves and produces angular displacement, the two laser beams will interfere when they meet, and the angular displacement of the object is measured by the interference fringe of the light, so as to calculate the angular speed of the object, thus completing the same task of the mechanical gyroscope. Its accuracy is much higher than the mechanical gyroscope, no moving parts, easy to maintain, high reliability, long life, so as to replace the mechanical gyroscope, become the core component of the inertia reference system of large and medium-sized aircraft, but it is larger than the mechanical gyroscope, the price is high, so it is used less in small aircraft.
4.Fiber optic gyro: The fiber optic gyroscope is a sensitive element based on the optical fiber coil, and the light emitted by the laser diode propagates along the optical fiber in two directions. Compared with laser gyroscope, fiber optic gyroscope has lower cost and is more suitable for mass production.
With the development of science and technology, the precision of low cost fiber optic gyro and micromechanical gyro is getting higher and higher, which is the general trend of the development of gyro technology in the future.
For more information, please feel free to contact info@ericcointernational.com
More Technical Questions
1.How accurate is MEMS gyroscope?
2.Where are MEMS Gyroscopes Used?
3.How do MEMS gyroscopes work?
4.Application of MEMS gyroscope in oil and gas field
5.The Principle of MEMS Gyroscope
6.Application of MEMS gyroscope in automobile automatic driving
Products in Article
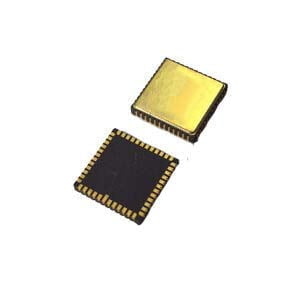
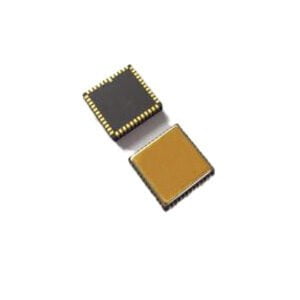
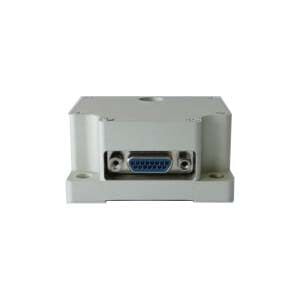
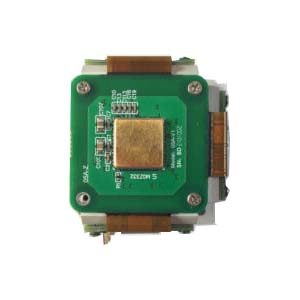
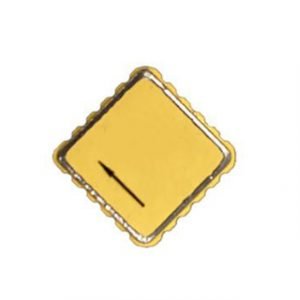
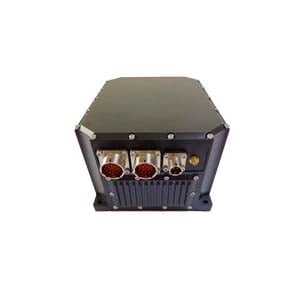