The ER-MG2-100 is a micromachined single-axis gyro sensor. ER-MG2-100 provides highly accurate north-seeking angular rate (gyroscope) measurement with market-leading low power consumption, the bias stability (Allan variance) is only 0.02°/h, and the bias stability (1σ 10s) is only is 0.1°/h. The ER-MG2-100 is optimized for high accuracy and stability. ER-MG2-100 is designed for north-seeking, advanced differential sensor design rejects the influence of linear acceleration. Angular rate data is presented as a 24-bit word. It is available in a hermetically sealed ceramic LCC surface mount package, and is capable of operating at 5V supply and a wide temperature range (−45°C to +85°C).
ER-MG2-100 is available in a compact 11 x 11 x 2mm package. When the gyroscope is in full operating mode, the power consumption is typically 40mA. ER-MG2-100 is mainly used in high-precision multi-axis applications such as oil drilling, automated driving, and aviation. It can be placed in IMU, north finder, gyrocompass, tool while drilling, and inertial navigation system. The gyroscope used in ERICCO's upcoming new MEMS IMU ER-MIMU-06 is ER-MG2-100, which will represent a major technological breakthrough in MEMS IMU in terms of high precision. So it is specially designed for north seeking, pointing, initial alignment in logging tools/gyro tools, mining/drilling equipment, weapon/UAV launch systems, satellite antenna,target tracking system and so on. Thanks to the high performance, ER-MG2-50/100 can also used in high precision attitude measuring, stabilization control, positioning, navigating in navigation grade MEMS IMU/ INS, land surveying/land mobile mapping system, railway train system, etc. So ER-MG2-50/100 is a best, cost effective, robust, reliable, small size, light weight, low power alternative of medium-low navigation grade FOG DTG with north seeking, precision attitude measuring , inertial positioning and navigation function.
The ER-MG2-100 is designed for north seeking applications. As an advanced differential sensor design, it rejects the effects of linear acceleration, enabling it to operate in extremely harsh environments where shock and vibration are present.
Application
1. Oil and gas field
Gyroscope measurement is an essential part of drilling, and the harshest use environment for gyroscopes is the oil and gas downhole drilling industry.
The ER-MG2-100 MEMS gyroscope uses a solid-state sensor design to withstand extreme conditions such as downhole shock and vibration without recalibration during use and consumes less energy. The same battery can last longer. The gyro MWD embedded in the ER-MG2-100 can meet the accuracy requirements required by today's complex drilling environment, and because of its high precision, when used in conjunction with MWD tools, the uncertainty can be reduced by 45%, which is conducive to precision Measurement.
2. Automobile automatic driving
The ER-MG2-100 instrument is a positioning module for the automatic driving function of the car. Autonomous vehicle positioning system usually consists of GPS module, three-axis acceleration sensor and three-axis gyroscope. Information obtained by combining sensors provides the vehicle with its position.
3. Aerospace
Because aerospace technology has very high requirements on the functional density ratio of devices. In aerospace and space applications, high-precision interferometric fiber optic gyroscopes are generally used.
MEMS ER-MG2-100 compared with FOG, ER-MG2-100 can reach the same high accuracy as FOG but it's much smaller in size, lower emission-quality and cheaper, low power to maintain temperature. It can be used for attitude and heading reference systems, flight control systems, modal testing, etc. in aerospace applications.
More Technical Questions
1.Development Status of China’s MEMS Industry
2.What is MEMS Sensor and its Technical Advantages?
3.Analysis of the main performance parameters of MEMS gyroscope
4.Background and Development Status of MEMS Inertial Sensors
6.Analysis of Typical Applications of MEMS Sensors
Products in Article
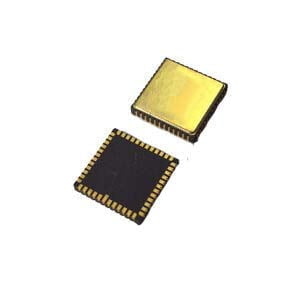
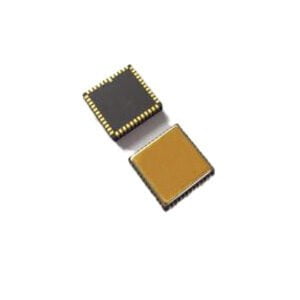
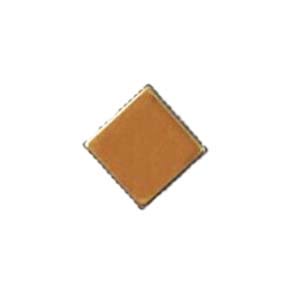
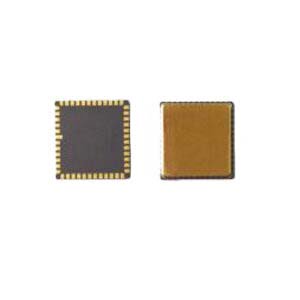
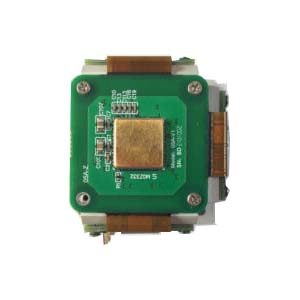
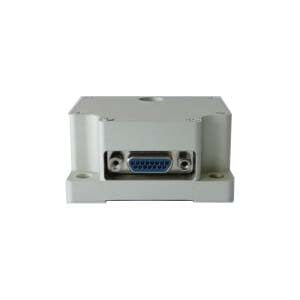