IMU is a sensor combination used to measure the motion state of an object, mainly composed of a gyroscope and an accelerometer. IMU is usually used in navigation, attitude control, motion tracking and other fields. By measuring the angular velocity and acceleration of an object in three axes, it can calculate the object's attitude, position, speed and other information. The error of MEMS-IMU often requires calibration, which is also important. Then its error can be divided into systematic error and random error. Systematic errors can be eliminated through sensor calibration, while random errors can be understood as the degree of fluctuation and drift of the zero bias. It is usually assumed that the zero bias noise of low-cost MEMS-IMUs obeys a Gaussian distribution. The modeling and compensation of systematic errors and random errors is now an important research direction.
System errors can be eliminated through hardware calibration and software compensation. Hardware calibration usually uses professional calibration equipment to calibrate the IMU, measure the output of each sensor and establish a calibration curve, so that the output can be corrected based on the calibration curve in subsequent use. Software compensation uses algorithms to correct the sensor output, such as using a Kalman filter to perform state estimation and error compensation on the IMU output.
For random errors, temperature compensation technology can be used to reduce them. Since the performance of MEMS sensors is affected by temperature, studying the effect of temperature on sensor output and compensating it is an important technology. Currently, common temperature compensation technologies include neural network compensation, support vector machine compensation, and polynomial fitting compensation. These technologies collect sensor output data at different temperatures, establish a mathematical model of temperature and sensor output, and compensate the sensor output in real time to reduce the impact of temperature on sensor performance.
In addition, in order to further improve the performance of MEMS-IMU, the error transfer function method can also be used to model and compensate the IMU error. This method analyzes the error transfer function of the IMU, establishes a mathematical model of the error transfer function, and compensates the IMU output according to the model. This method can more comprehensively consider the impact of various factors on IMU performance, thereby more accurately estimating the IMU's output and making compensation. This article will talk about MEMS IMU error modeling and MEMS IMU temperature compensation technology.
1.MEMS IMU error modeling
The error modeling of MEMS IMU (Inertial Measurement Unit) mainly focuses on the quantitative description of various error sources in the IMU. These error sources mainly include scale factor error, cross-coupling error, zero bias instability, etc.
The scale factor error and cross-coupling error can be expressed in matrix form and are related to the noise spectrum of the gyroscope and accelerometer. These errors average to zero over time, but any asymmetry or nonlinearity in the scale factor and cross-coupling error will form part of the vibration error and will not cancel each other out over time.
In addition, random errors are also an important source of MEMS IMU errors, mainly including quantization noise, angle (velocity) random walk, bias instability, angular rate (acceleration) random walk and rate ramp, etc. Among them, angle (velocity) random walk and zero-bias instability are the main manifestations of MEMS IMU.
In order to reduce these errors, various compensation methods can be used. For example, system errors are eliminated through hardware calibration and software compensation, and the impact of random errors is reduced through temperature compensation technology. Temperature compensation technology can collect sensor output data at different temperatures, establish a mathematical model of temperature and sensor output, and compensate the sensor output in real time based on the model.
In addition, the error transfer function method can also be used for error modeling of MEMS IMU. By analyzing the error transfer function of the IMU, a mathematical model of the error transfer function is established, and the output of the IMU is compensated based on the model. This method can more comprehensively consider the impact of various factors on IMU performance, thereby more accurately estimating the IMU's output and making compensation.
In general, error modeling of MEMS IMU is a complex process that requires comprehensive consideration of multiple factors and methods. Through in-depth understanding and research of sensor performance, continuous optimization of compensation algorithms and improvement of manufacturing processes, the performance and reliability of MEMS IMU can be improved, providing important technical support for the development and application of navigation, positioning, attitude control and other fields.
2.MEMS IMU temperature compensation technology
The temperature compensation technology of MEMS IMU mainly studies the impact of temperature on sensor performance and takes corresponding methods to reduce this impact. The following are several common temperature compensation methods:
2.1 Hardware Calibration and Compensation: By calibrating the IMU during the manufacturing process, the output of each sensor is measured and a calibration curve is established. In actual use, the output of the IMU is corrected according to the calibration curve to reduce the impact of temperature on sensor performance.
2.2 Establish a mathematical model: By collecting the output data of the sensor at different temperatures, establish a mathematical model of temperature and sensor output. This model is used to compensate the sensor output in real time to reduce the impact of temperature on sensor performance. Common mathematical models include polynomial fitting, linear regression, and neural networks.
2.3 Error transfer function: By analyzing the error transfer function of the IMU, a mathematical model of the error transfer function is established. Compensating the output of the IMU based on this model can more comprehensively consider the impact of various factors on the performance of the IMU, thereby more accurately estimating the output of the IMU and performing compensation.
2.4 Dynamic adjustment: In some cases, the impact of temperature on sensor performance can be reduced by dynamically adjusting the operating parameters of the IMU. For example, by adjusting parameters such as sampling frequency and gain, the performance of the IMU at different temperatures can be made more stable.
In summary, temperature compensation technology for MEMS IMUs requires selecting an appropriate method based on the specific situation. Through in-depth understanding and research of sensor performance, continuous optimization of compensation algorithms and improvement of manufacturing processes, the performance and reliability of MEMS IMU can be improved, providing important technical support for the development and application of navigation, positioning, attitude control and other fields.
Summarize
In general, research on IMU error modeling and temperature compensation technology based on MEMS is an important research direction. By in-depth study of the error sources and characteristics of MEMS-IMU, and using appropriate calibration and compensation methods to reduce the impact of errors, the performance and reliability of MEMS-IMU can be improved, providing information for the development and application of navigation, positioning, attitude control and other fields. Important technical support. As a company that independently researches inertial systems, ERICCO has conducted in-depth research on MEMS IMUs. For example, the navigation-grade ER-MIMU-01 and ER-MIMU-02 can independently seek north, and the built-in gyroscopes and accelerometers are also highly accurate. If you are interested in our IMU, please click on the article link below to learn more.
More Technical Questions
1.Calibration method and error analysis of low-precision MEMS IMU
2.MEMS-IMU error calibration compensation method that does not rely on precision turntable
3.Application of Improved Wavelet De-noising Method in MEMS-IMU Signals
4.Research on error modulation technology of MEMS based on IMU rotation
5.Research on MEMS-IMU signal denoising technology
Products in Article
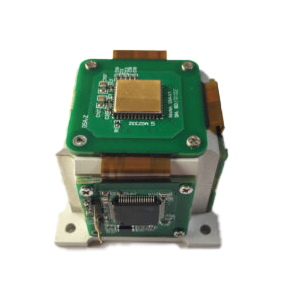
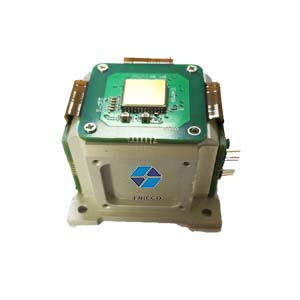
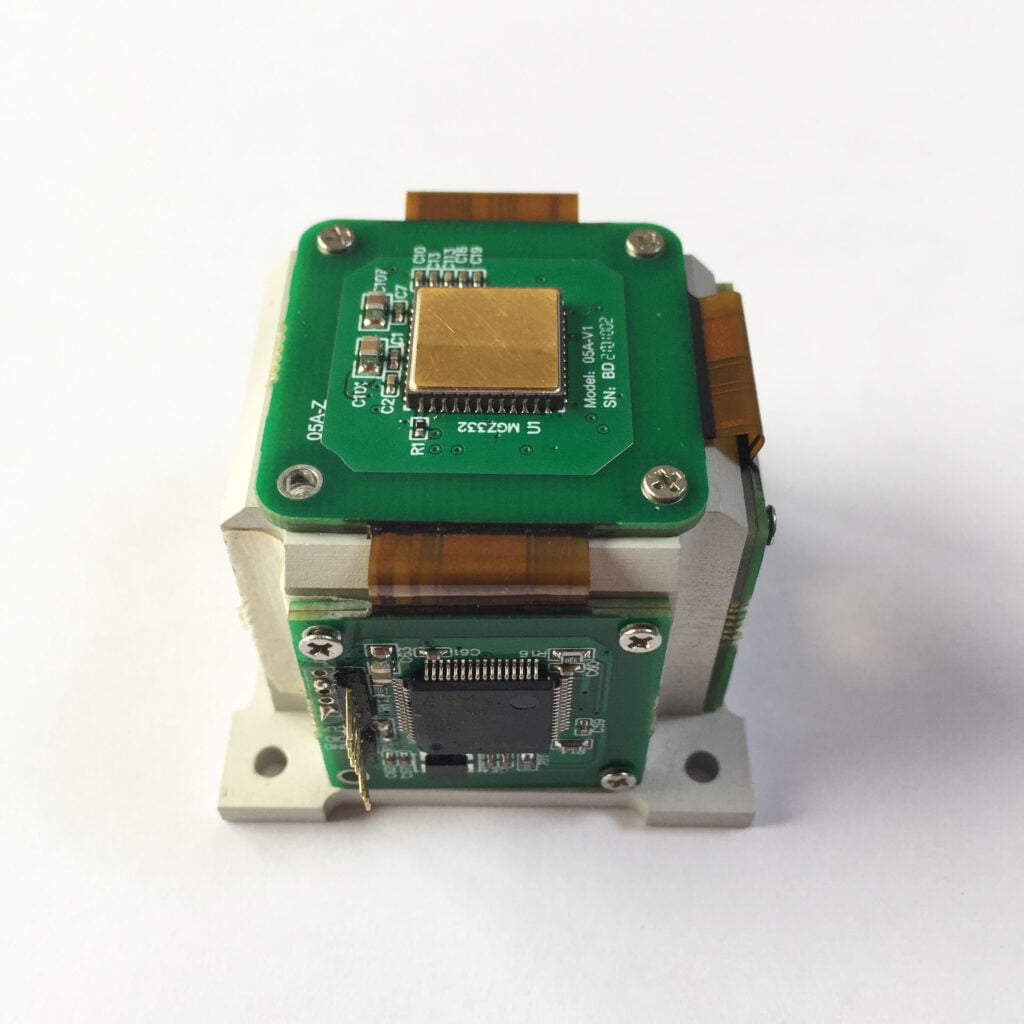
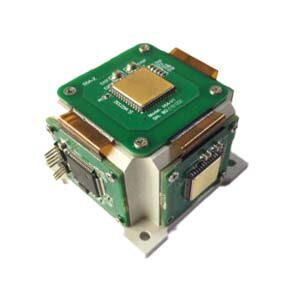
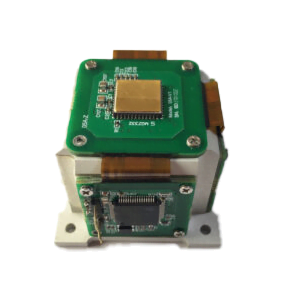
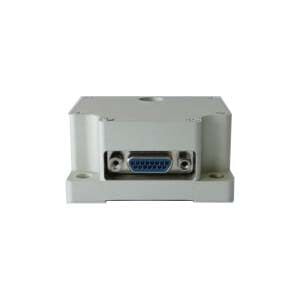