With the continuous improvement of MEMS sensor, the advantages of small size and light weight of MEMS gyroscope have been further highlighted, and their application fields have been rapidly expanded. MEMS gyroscope can be used to detect the angular rate of the carrier's three axes and determine the carrier's attitude, which is the basis and core key component of carrier navigation.
For MEMS gyroscope based on Coriolis effect, Coriolis force will be generated when the resonant gyroscope sensitive mass block is subjected to the input angular velocity perpendicular to the two-dimensional plane of the drive axis and the detection axis, which causes the mass block to vibrate simply along the direction of the detection axis, and the amplitude of vibration is proportional to the vibration velocity of the drive axis and the input angular velocity. As shown in Figure 1, the X axis is the drive axis of the gyroscope, the Y axis is the detection axis of the gyroscope, and the Z is the sensitive axis of the gyroscope.
Figure 1 Dynamic model of MEMS gyroscope
The sensitive structure of MEMS gyroscope involved in this study is designed with a four-mass tuning fork symmetrical structure, and the input angular rate Ω0 in the vertical plane is measured. The vibration masses M1, M2, M3 and M4 are sensitive units capable of vibrating at x and y degrees of freedom. The vibration in the x direction produces the motion velocity, which interacts with the angular rate input Ω0 to produce the Coriolis acceleration in the y direction. The vibration mass is subjected to Coriolis inertia force in y direction and produces forced vibration. The amplitude of the vibration in the y direction represents the Coriolis acceleration, and the measured value of the angular rate output is obtained by further calculation. The sensitive structural modes of the gyroscope are shown in Figure 2.
Figure 2 Modal simulation diagram of gyroscope sensitive structure
The MEMS sensor is driven by electrostatic force to do simple vibration, and the amplitude of simple harmonic vibration is directly related to the magnitude of electrostatic force. The electrostatic force is inversely proportional to the square of the plate spacing, proportional to the plate area, and proportional to the square of the voltage. In order to make the device under AC drive, according to the desired frequency, that is, vibration with the same frequency as the drive voltage, the applied voltage is generally used, including DC components and AC components. In order to keep the normal electrostatic force only the fundamental frequency component, the voltage applied at both ends of the movable electrode by the push-pull method is as follows:
V2=Vc + Vasin wt
V2=Vc - Vasin wt
In the formula, V1 and V2 are the voltage applied at both ends of the movable electrode, Vc is the DC component, Va and w are the amplitude and frequency of the AC component, then V1 normal electrostatic force includes a fundamental frequency term independent of displacement and a linear term related to displacement. MEMS sensor is based on flat plate capacitance tangential driving force and adopts push-pull drive. The simplified driving comb tuning fork structure is shown in Figure 3.
Figure 3 Schematic diagram of comb capacitor structure
The voltage applied on the left and right fixed electrodes is V1 and V2 respectively, and the electrostatic driving force is generated:
Where Nd is the logarithm of comb teeth, d0 is the distance between plates, h is the thickness of plates, and ε is the dielectric constant of the medium between plates. As can be seen from the above formula, tangential electrostatic force is directly proportional to plate thickness and comb log, and inversely proportional to plate spacing.
The capacitance detection of the detection shaft is to detect the displacement of the mass block by the change of the relative position of the two plates of the capacitor. The principle is the opposite of what happens when it is driven. The sensitivity and displacement of parallel plate capacitors are linear in Z and Y direction, and quadratic in X direction. Therefore, in the X-axis direction, when subjected to force or linear acceleration, the sensitive mass block will be biased in the X direction of the drive shaft, resulting in an increase in the driving force of the drive shaft and a larger resonant speed. In the case of the same angular rate input, the measurement output of the gyroscope will increase accordingly. When there is an external force on the Y axis or Z axis, it will cause the displacement change of the detection axis plate, which will cause the measurement output error of the gyroscope. Under the action of external force or linear acceleration in space triaxial, the gyroscope will inevitably produce output errors.
This paper introduces the error generation mechanism of MEMS gyroscope under the condition of high acceleration. Under the environment and its own conditions, there will be some errors in the gyroscope, which needs to be corrected by strict calibration methods. The knowledge of gyroscope calibration can be learned by reading the previous articles. With its rich experience in the production and development of MEMS gyro, not only for single-axis gyro, Ericco also has a professional two-axis and three-axis MEMS gyro product line. For example, ER-2MG-01 is a north seeking two-axis MEMS gyroscope, which can achieve attitude measurement function. The ER-3MG-02 is a navigation three-axis MEMS gyroscope that can be used for system development.
If you are interested in other information about MEMS sensor, please contact us.
More Technical Questions
1.Bandwidth test method of MEMS gyroscope
2.Impact resistance technology of MEMS gyroscope
3.Research on driving mode of MEMS gyroscope
4.Research on scale factor nonlinearity of MEMS gyroscope
5.Bias Temperature Compensation Analysis of MEMS Gyroscope
6.System error and calibration of MEMS gyroscope
Products in Article
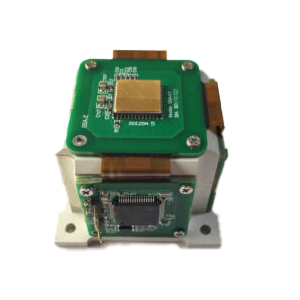
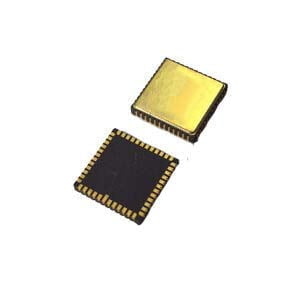
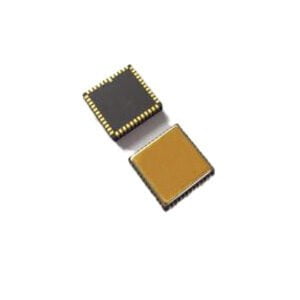
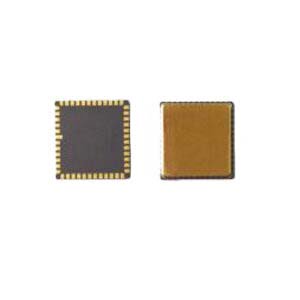
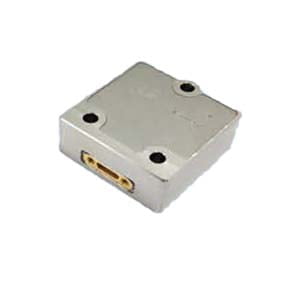
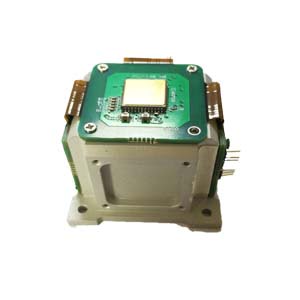