Q-Flex accelerometer is a kind of inertial measurement device, which utilizes the quartz pendulum to measure the acceleration of the object by the characteristic of deviating from the equilibrium position by the inertial force. Thanks to the low temperature coefficient of high-purity quartz material and stable structural characteristics, Q-Flex accelerometer has high measurement accuracy, low measurement noise, good long-term stability, and is widely used in attitude control, navigation and guidance of aircraft, as well as geological exploration and other industrial environments.
1.Detection method for Q-Flex Accelerometer
When the system is open-loop, because the system can not produce feedback moment, the pendulum assembly is subjected to weak inertia moment or the active moment of the torque converter, the quartz pendulum easily touches the yoke iron and saturated phenomenon, which makes it very difficult to test the damping parameters under the open-loop, therefore, the damping parameters are considered to be measured under the closed-loop state of the system.
The closed-loop frequency characteristics of the control system reflect the variation of the amplitude and phase of the output signal with the frequency of the input signal. The frequency response of the stabilized system is at the same frequency as the input signal, and its amplitude and phase are functions of the frequency, so the amplitude-phase characteristic curve of the frequency response can be applied to determine the mathematical model of the system. In order to obtain the actual damping parameters of the accelerometer, the closed-loop frequency response measurement method is used.
In the closed-loop frequency response measurement method, the accelerometer is fixed on the horizontal vibration table in the "pendulum" state, so that the acceleration input direction of the vibration table is aligned with the sensitive axis of the accelerometer and the accelerometer is placed horizontally in the "pendulum" state, which can eliminate the asymmetry of the gravitational force on the input acceleration. The horizontal placement of the accelerometer in the "pendulum state" eliminates the effect of gravity on the asymmetry of the input acceleration.
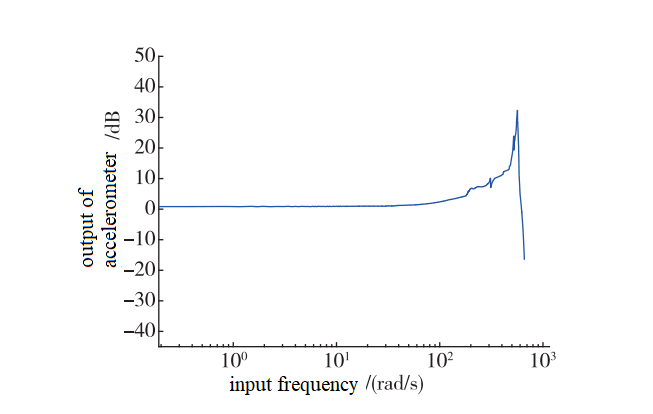
By controlling the horizontal shaker, a sinusoidal acceleration signal of 6 g (g is the acceleration of gravity, 1 g ≈ 9.8 m/s2), with a gradually increasing frequency from 0 to 600 Hz, is applied to the Q-Flex accelerometer, which can reflect the amplitude attenuation and phase delay of the output of the accelerometer within the design range and bandwidth of the accelerometer. Accelerometer will produce the corresponding output under the action of the shaking table, the high sampling rate recorder connected to both sides of the sampling resistance, recording the output of the accelerometer, and plot the amplitude-frequency characteristic curve shown in Figure 1.
In the passband of the accelerometer amplitude-frequency characteristic curve, the quartz flexural accelerometer maintains a good acceleration following ability, with the increase of the input acceleration frequency, the system resonance peak at 565Hz, the resonance peak is Mr=32dB, the cutoff frequency of the system is 582Hz, the amplitude of the system at the frequency began to produce more than 3dB of attenuation. Since the rotational inertia, stiffness and the rest of the parameters of the servo control loop of the Q-Flex accelerometer are known, the amplitude-frequency characteristics of the system are used to solve for the unknown parameter δ. The closed-loop transfer function of the system is given as
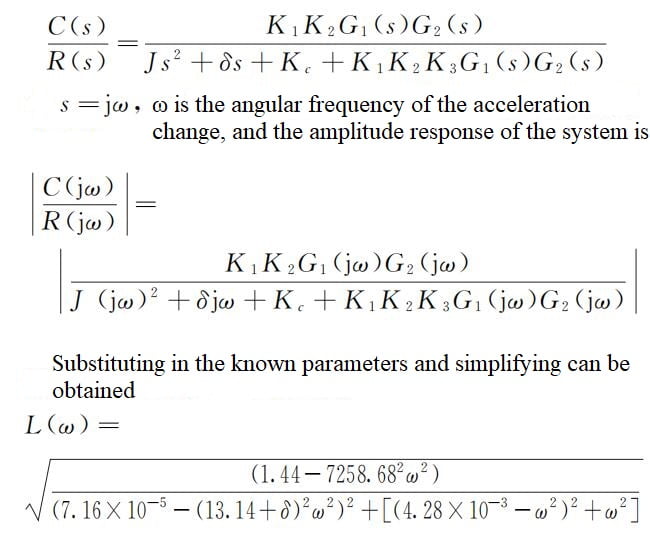
The least-squares method estimates the parameters of the model based on the actual observed data, and a set of frequency amplitude data is obtained by generating an external acceleration input through a horizontal shaker, which is measured by a pen register, as shown in Table 1.
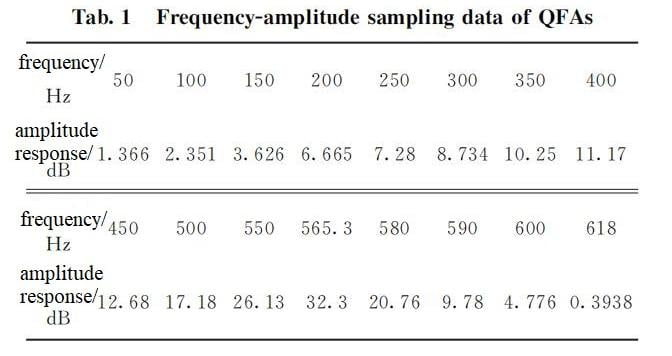
The amplitude-frequency response function of the quartz flexural accelerometer system with known parameters is the objective function, and the residual sum of squares with unknown parameters is established as

Where, n is the number of selected feature points. Using the above equation, a suitable value of δ is selected so that D(δ) has the minimum value. The desired damping coefficient is obtained as δ=7.54×10-4N·m·s/rad using least squares fitting.
The closed-loop simulation model of the system is established, and the damping coefficient is substituted into the quartz flexural accelerometer head model and the system is simulated, and the amplitude-frequency characteristic curve of the system is plotted as shown in Fig. 2, which is closer to the measured curve.
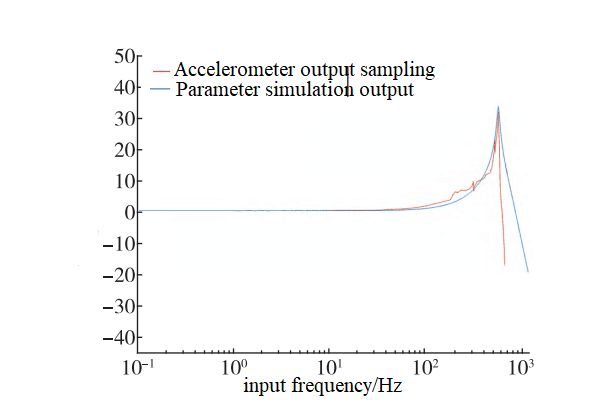
Some studies have solved the damping distribution of the piezoelectric film on the surface of the pendulum by the finite time domain difference method, and the damping coefficient of the piezoelectric film of the pendulum is 1.69×10-4N·m·s/rad, which indicates that the damping coefficient obtained by the system amplitude-frequency response identification has the same order of magnitude as the theoretical calculated value, and the error originates from the damping of the material of the mechanical structure, the mounting error during installation and testing, the input error of the shaker, and other environmental factors. environmental factors.
2.Conclusion
Ericco provides high-precision quartz accelerometers, such as ER-QA-01A3, with small error and high precision, which have a bias stability of 10μg, scale factor repeatability of 10ppm, and a weight of 80g, and can be widely used in the fields of oil drilling, carrier microgravity measurement system, and inertial navigation.
More Technical Questions
1. Full-temperature Performance Optimization Method For MEMS accelerometer
2. Temperature Compensation Method for Q-Flex Accelerometers
3. Driving Automotive Evolution: MEMS Accelerometers
4. Factors Affecting the Stability of Q-Flex Accelerometers
5. Structure Design of High Precision Quartz Flexible Accelerometer
6. Methods to Maintain the Long-Term Performance of Quartz Flexure Accelerometers