The quartz flexible accelerometer is one of the key sensitive components in inertial navigation systems, and its measurement error directly affects the accuracy of the entire navigation system.
In the quartz flexible accelerometer, the measurement error is directly related to its own bias (K0) and scale factor (K1). However, during storage and usage, the K0 and K1 of the quartz flexible accelerometer undergo complex drift over time due to internal and external factors, making it difficult to accurately describe them, thus seriously affecting the stability of the quartz flexible accelerometer.
This article analyzes the factors affecting parameter stability from two aspects: parameter time stability and environmental stress stability.
1.Major Components and Materials:
The structure of the quartz flexible accelerometer is decomposed, as shown in Figure 1.
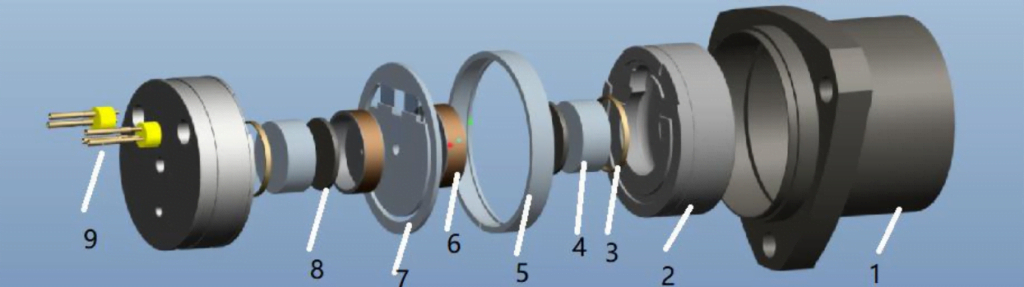
1-housing, 2-flexible magnet, 3-preload ring, 4-magnet, 5-isolation ring, 6-torque coil, 7-quartz pendulum, 8-flange, 9-servo circuit
2.Bias Stability Analysis
2.1 Bias:
Bias refers to the output value of the quartz flexible accelerometer when the input is zero. Constant interference torque in the header structure, electromechanical bias angle, and input offset of the sensor detection circuit are the main factors causing bias. The internal principle of these factors affecting bias is shown in Figure 2.

Mo represents the constant disturbance torque, β is the interference of the elastic recovery angle, and Uo is the offset at the input end of the amplifier. After incorporating each influencing factor into the static block diagram, the transfer function is calculated to obtain the expression for zero offset. The zero offset expression can be analyzed from the equation. Simplifying the transfer function yields Formula 1.
From Formula 1, it can be inferred that the generation of the offset is caused by the respective actions of the constant disturbance torque Mo, the interference of the elastic recovery angle, and the disturbance at the input end of the amplifier Uo on the quartz flexible accelerometer.
From Eq.1, it can be seen that when the three components of constant value disturbance moment Mo, elastic recovery angle disturbance, and amplifier input disturbance Uo act on the quartz flexure accelerometer respectively, they lead to the generation of bias.
2.2 Influence factors of bias time stability:
Considering the reasons for bias, the basic technology of quartz flexible accelerometers, and the characteristics of their manufacturing process, the factors affecting the bias time stability of quartz flexible accelerometers can be determined as follows:
(1) Residual stress release:
The core structure of the quartz flexible accelerometer is composed of upper and lower torque generators and a pendulum assembly. During assembly, a laser welding process is used to connect the preload ring with the upper and lower soft magnetic bodies to fix the pendulum assembly between them.
However, the thermal stress brought about by laser welding in the long time after the completion of the processing of the release of the obvious, will bring about a change in the zero position of the differential capacitance sensor, the bias value of the accelerometer will change to affect the stability of its own bias value.
The performance of quartz flexure accelerometer is largely determined by the quality of quartz pendulum. Quartz pendulum processing process of ten procedures will bring different processing stress and thermal stress, with the change of time, these stresses in the process of releasing the flexural flat bridge will appear in an elastic recovery angle, the zero position will therefore change to affect the bias stability.
The relationship between the preload change and the bias stability is simulated and analyzed, and the stress change of the flexible flat bridge of the pendulum assembly is simulated when the preload is reduced due to the release of the stress, and the results are shown in Fig. 3. From the figure, it can be seen that when the preload force changes by 10N, about 100μg bias repeatability change is produced.
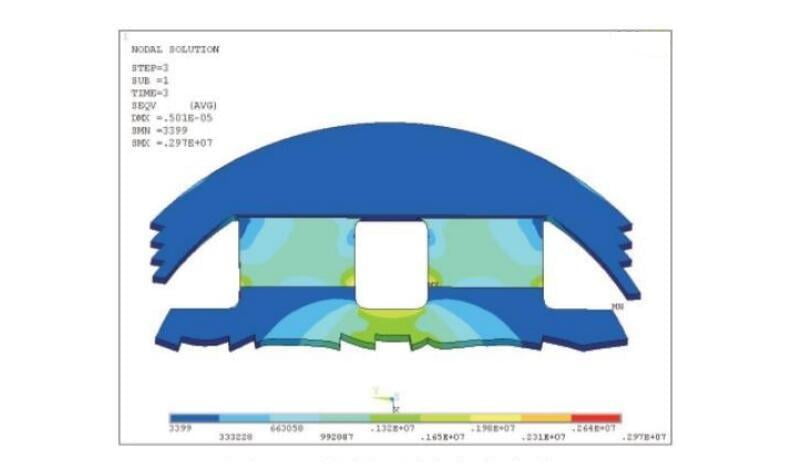
(2) Assembly stress relief:
In the header structure of the quartz flexible accelerometer, to fix the upper and lower structures together and minimize changes in preload force on the excitation ring, only belly bands can be used for bonding at the junction of the upper and lower excitation rings.
Currently, bonding is done manually without applying pressure, leading to two issues: uneven application of epoxy adhesive, resulting in asymmetric bonding areas and uneven adhesion stresses on the upper and lower sides; and natural curing of the epoxy adhesive, resulting in lower bonding strength, insufficient contact, and low adhesion at the metal junction. Over time, changes in preload force at the bonding site occur.
These two issues, evolving over time, both affect the stability of the bias.
Moreover, while the design of the header structure of the quartz flexible accelerometer adopts a symmetric upper and lower structure, limitations in the assembly process can result in asymmetric internal stresses. As these asymmetrical stresses are released over time, slight deformations or movements occur in the upper and lower excitation rings relative to the pendulum assembly's position, causing changes in the zero position of the differential capacitive sensor and affecting zero bias stability.
(3) Zero drift of the integral amplifier:
The bias of the integral amplifier can be converted to the input of the operational amplifier, which is equivalent to the zero drift of the sensor detection circuit. As time changes, the zero drift of the integral amplifier affects the stability of the bias value.
3.Scale factor time stability analysis
3.1 Scale Factor:
Based on the process of converting sensed acceleration into electrical signals by the quartz flexible accelerometer, it is known that under force balance conditions, the input-output relationship of the quartz flexible accelerometer is:
m is the mass of the pendulum assembly; L is the length from the flexure pivot to the center of mass of the pendulum assembly; K1 = mL/Ktg scale factor, is the feedback current required at the input unit acceleration.
From the equation, the scale factor of the quartz flexure accelerometer is determined by the pendulum's oscillation and the torque generator coefficient.
3.2 Internal influences on the time stability of the scale factor:
From the above analysis, it can be seen that with the change of time when the structure of the momenter and the pendulum changes, the scale factor will change. Therefore, inside the quartz flexure accelerometer there are two main influences on the scale factor time stability:
(1) Magnet aging:
With the change of time, quartz flexural accelerometer head structure in the magnetic steel air gap magnetic performance will be reduced that is, magnetic steel aging, magnetic steel air gap magnetic induction strength depends mainly on the relative permeability of the magnetic steel. The relative permeability of the magnet steel changes with time and temperature as shown in Figure 4.
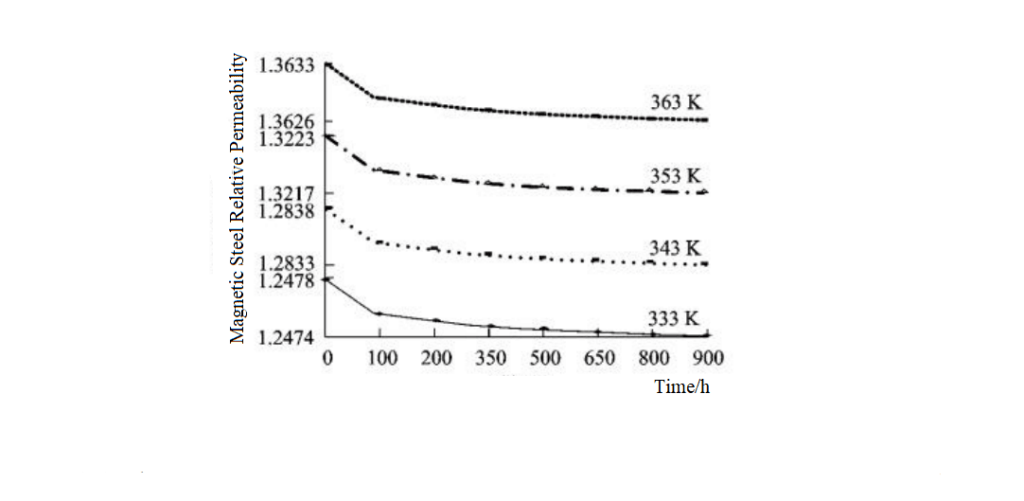
Figure 4 shows that the relative permeability of the magnet steel with the change of time will be reduced, which will lead to changes in the working air gap flux density B will lead to a reduction in the stability of the moment coefficient Ktg, which in turn affects the stability of the scale factor.
(2) Epoxy glue creep:
The pendulum assembly is made from the torque converter coil along with the aluminum skeleton bonded to the pendulum by means of adhesive. The structure of the pendulum assembly changes with time when the epoxy glue creeps, and the test results of epoxy glue creep versus time are shown in Figure 5.
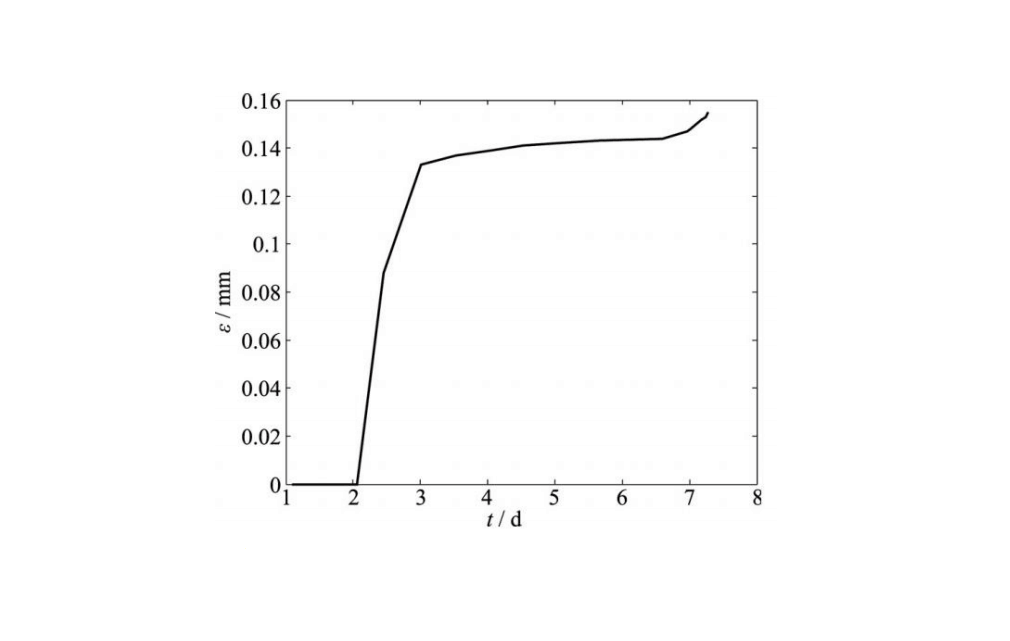
It can be seen from Figure 5 that the amount of creep of the adhesive increases with time, which causes the torque converter coil to move slightly at the glue joint. At this point the length between the center of mass and the flexure pivot will change due to the change in the position of the center of mass of the quartz pendulum assembly, resulting in a change in the pendulum properties affecting the stability of the scale factor.
Additionally, in the torque generator assembly, internal stress release and epoxy adhesive creep at the bonding site cause slight movements between the components of the torque generator structure. As a result, changes in the position of the axis of the torque applied by the coil occur due to alterations in the magnetic field distribution, affecting the length from the axis of torque application to the flexure pivot and consequently influencing the stability of the scale factor.
4.Analysis of parameter time stability influencing factors
Through the above analysis, the main influencing factors of parameter time stability are determined, as shown in Table 1.
5.Conclusion
The article discusses the importance of quartz flexible accelerometers in inertial navigation systems and how their measurement errors impact system accuracy. It highlights factors affecting parameter stability, including zero offset and scale factor time stability. Factors such as residual stress release, assembly stress release, magnetic steel aging, and epoxy creep are analyzed. Understanding and managing these factors are crucial for maintaining the stability and accuracy of quartz flexible accelerometers in navigation systems.
It is worth noting that the high-performance ER-QA-03A series of accelerometers use high-quality quartz crystals, capable of adapting to high-temperature, high-pressure, high-vibration environments, and various environmental conditions with high acceleration applications, exhibiting extremely high reliability and stability.
In addition, the ER-QA-03A1 accelerometer have a scale factor of 15 ppm and bias repeatability of 10 μg, achieving high-precision measurements. Apart from extensive applications in aerospace and military fields, it is also widely used in automotive, medical, and research fields. In scientific research, it can be used for studying earthquakes, crustal movements, cosmology, and microgravity environments.
More Technical Questions
1. Structure Design of High Precision Quartz Flexible Accelerometer
2. In-Depth Exploration: What Exactly is Satellite Timing?
3. Methods to Maintain the Long-Term Performance of Quartz Flexure Accelerometers
4. Analysis of Temperature Characteristics of Quartz Flexible Accelerometer
5. MEMS Accelerometers for Analyzing Mechanical Vibrations
6. Maximizing GNSS Applications in Land Vehicles Systems
Products In Article

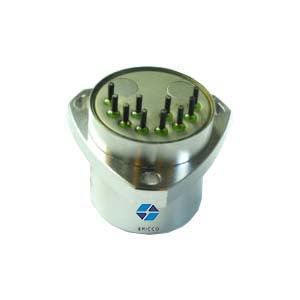
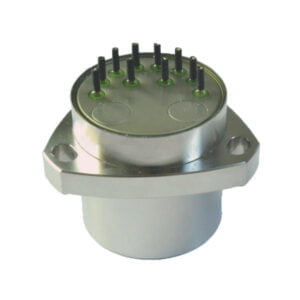
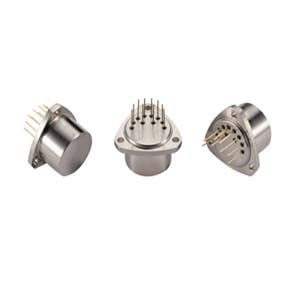
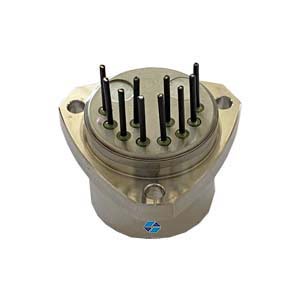
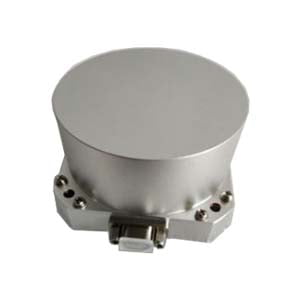