IMU is a sensor combination used to measure the motion state of an object. It usually consists of three gyroscopes and three accelerometers, which can measure the angular velocity and acceleration of an object in three axes, and then calculate the attitude, position, speed and other information of the object.
In reusable spacecraft, the dynamic accuracy of the IMU is crucial to ensure the stability and navigation accuracy of the spacecraft. Dynamic accuracy evaluation is an important means to test the performance of IMU, which can reflect the error size and change pattern of IMU in the actual working environment. Therefore, effective evaluation methods are needed to comprehensively evaluate the dynamic accuracy of IMU.
Dynamic accuracy assessment methods usually include steps such as data collection, data preprocessing, error calculation, error law analysis, optimization plan formulation, and optimization effect verification. These methods help discover potential problems with the IMU and provide a basis for optimizing the design and manufacturing process, thereby improving the navigation accuracy and stability of the spacecraft.
In summary, the dynamic accuracy assessment of IMUs is critical to the performance of reusable spacecraft. Through scientific and reasonable evaluation methods, we can comprehensively understand the performance of the IMU, provide a basis for optimizing the design and manufacturing process, and improve the navigation accuracy and stability of the spacecraft.
1.Reusable spacecraft
A reusable spacecraft needs to undergo launch ascent, long-term orbit and re-entry and return during its mission cycle. Among them, there is no optical measurement sensor available during the reentry and return stage, and the inertial measurement unit (IMU) must be relied upon to complete high-precision navigation. Since the reentry and return process requires a harsh random vibration dynamic environment, the dynamic characteristics of the IMU in the vibration environment become A key performance. In the indicator system of inertial measurement equipment, frequency characteristics are the key indicators to ensure the dynamic performance of a single machine. The reusable spacecraft puts forward amplitude frequency and phase frequency requirements for the IMU similar to those shown in Figure 1, in which the ⁃3dB cut-off frequency reaches about 100 Hz. In order to meet this demand, the reusable spacecraft is equipped with multiple sets of IMUs composed of optical gyroscopes (mainly fiber optic gyroscopes and laser gyroscopes) + quartz flexible accelerometers, and are integrated and used through system redundancy algorithms. Although optical gyroscopes have better inherent dynamic characteristics advantages than electromechanical gyroscopes, as a general-purpose product, optical gyroscopes have been widely used in many fields such as weapons, transportation, and space, and different products have been developed to meet the needs of various fields. Spectrum products. For aircraft such as satellites used in space environments, there is generally no need to pay attention to the dynamic characteristics of inertial measurement equipment in a mechanical vibration environment. Therefore, the corresponding spectrum products are often not specifically designed for frequency characteristics, or even relax their requirements for other accuracy indicators. Require. For reusable spacecraft that have both long-term on-orbit flight requirements and re-entry and return requirements, IMU products need to be adaptively improved on the basis of existing space products to take into account both on-orbit and return requirements.
2.Reusable spacecraft IMU dynamic accuracy evaluation method
The reusable spacecraft IMU dynamic accuracy evaluation method mainly includes the following steps:
2.1**Data collection**: Under different stages and conditions of spacecraft operation, accelerometer and gyroscope data are collected through the IMU sensor. These data will be used for subsequent accuracy evaluation.
2.2**Data preprocessing**: Perform preprocessing such as filtering and denoising on the collected raw data to eliminate outliers and noise and improve the accuracy of the data. This step is crucial for subsequent error calculations.
2.3**Error calculation**: Compare the preprocessed IMU data with the data provided by the ground station or other high-precision navigation systems to calculate the dynamic error of the IMU. These errors include accelerometer errors and gyroscope errors, which can be calculated and evaluated separately.
2.4**Error pattern analysis**: Analyze the calculated dynamic error to find out the error change patterns and influencing factors. For example, you can analyze the changing trend of errors over time, error distribution under different working conditions, etc. This step helps to deeply understand the performance of the IMU and provides a basis for optimizing the design and manufacturing process.
2.5**Optimization plan formulation**: Based on the error analysis results, formulate a targeted optimization plan. Optimization solutions may include improving the IMU manufacturing process, optimizing sensor layout, adjusting filter parameters, etc. These measures are designed to improve the dynamic accuracy and stability of the IMU.
2.6**Optimization effect verification**: After implementing the optimization plan, collect IMU data again and calculate the dynamic error to verify the optimization effect. If the optimization effect is good, the method can be reused; otherwise, the optimization plan needs to be re-formulated and verified.
Summarize
Through the above evaluation methods, the dynamic accuracy of the reusable spacecraft IMU can be comprehensively evaluated, potential problems can be discovered and effective measures can be taken for optimization, thereby improving the navigation accuracy and stability of the spacecraft. These methods can also provide reference for other similar sensor system evaluations. As a developer and manufacturer of IMUs, Ericco has adopted strict control measures for the dynamic accuracy evaluation of MEMS IMUs. In particular, the navigation-grade ER-MIMU-01 and ER-MIMU-02 have excellent accuracy and high calibration accuracy. Among them, the gyroscope has high accuracy, and the bias instability can reach 0.01-0.02°/hr and 0.03-0.05°/hr respectively.
If you are interested in other knowledge about MEMSIMU, please click the link below to learn more.
More Technical Questions
1.MEMS-IMU error calibration compensation method that does not rely on precision turntable
2.Application of Improved Wavelet De-noising Method in MEMS-IMU Signals
3.Research on error modulation technology of MEMS based on IMU rotation
4.Research on MEMS-IMU signal denoising technology
6.IMU self-calibration based on factorization
Products in Article
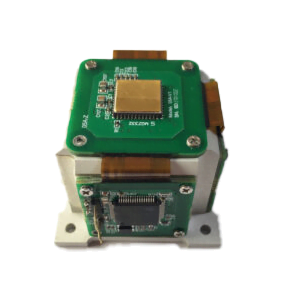
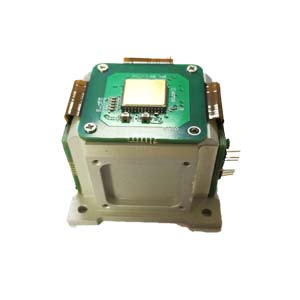
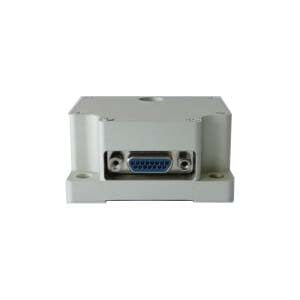
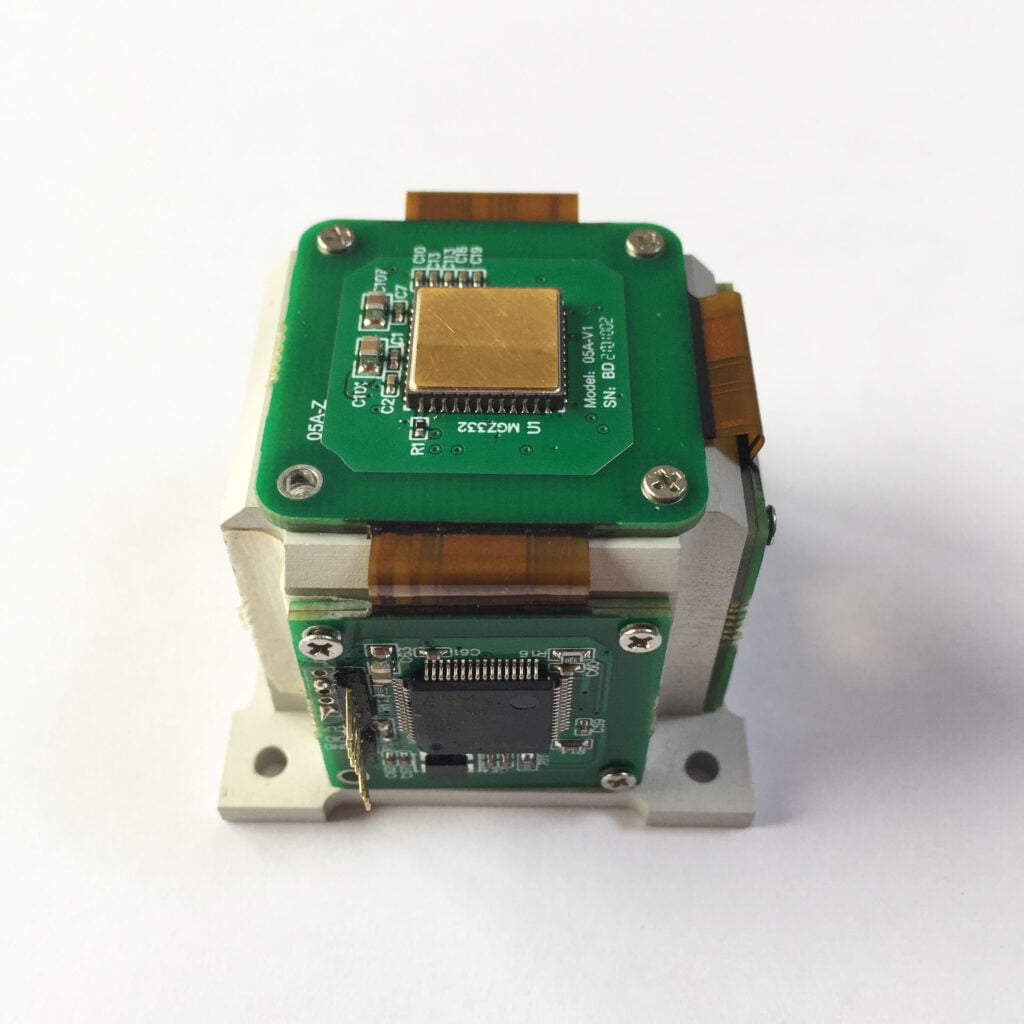
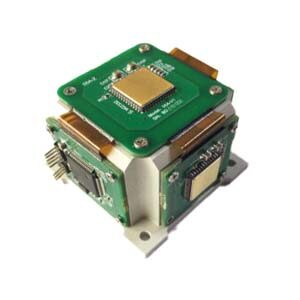
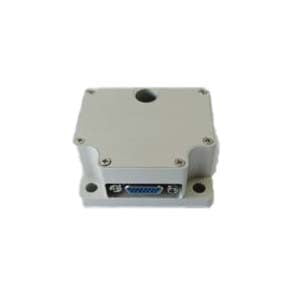