MEMS IMU (Inertial Measurement Unit) is a key component used for navigation and attitude measurement in many fields, such as aviation, aerospace, robotics, autonomous driving, etc. However, due to limitations in the manufacturing process, materials, and environment of MEMS IMUs, there are usually errors in its output data, and these errors will affect the accuracy of navigation and attitude measurement.
Error analysis and compensation help improve the measurement accuracy of MEMS IMU and ensure the accuracy of navigation and attitude measurement. By analyzing the sources of errors, we can gain an in-depth understanding of the error-generating mechanism and take effective compensation measures. These compensation measures can include hardware improvements, algorithm optimization, data fusion and other technologies.
In practical applications, MEMS IMU error analysis is also indispensable. For example, in the aviation field, IMU is used to provide attitude and navigation information of aircraft. Error analysis can help pilots or automatic control systems more accurately perceive the position and attitude of aircraft, thereby improving flight safety and navigation accuracy. In the field of robotics, IMU is used to provide attitude and position information of the robot. Error analysis can help the robot perceive its own status more accurately and thus perform tasks better.
To sum up, MEMS IMU error analysis and compensation are of great significance for improving measurement accuracy, ensuring the accuracy of navigation and attitude measurement, and enhancing safety. Therefore, error analysis and compensation are an integral part of MEMS IMU applications.
1.Error sources of MEMS IMU
The error sources of MEMS IMU mainly include systematic errors and random errors. Figure 1 shows the main error sources of MEMS IMU.
Figure1.MEMS IMU error sources
2.Error analysis of MEMS IMU
MEMS IMU (Inertial Measurement Unit) error analysis and compensation play an important role in improving the performance of navigation and attitude measurement systems. Error sources include systematic errors and random errors, which have varying degrees of impact on the output data of the IMU.
2.1 System error
System errors include errors of the sensor itself and errors caused by external factors such as temperature, humidity, etc. These errors usually appear as fixed deviations or repeatability errors, which can be reduced or eliminated through calibration and compensation techniques. Calibration is performed by testing the IMU in a series of known motion states, recording its output data, and then using these data to calculate the error coefficient of the IMU. Compensation is to correct the IMU output data based on these error coefficients to reduce or eliminate errors.
2.2 Random error
Random errors are errors caused by various random factors, such as sensor internal noise, vibration, etc. These errors are random and uncertain and difficult to completely eliminate. In order to reduce the impact of random errors on the IMU output data, filtering algorithms can be used to smooth the IMU output data, such as Kalman filters or complementary filters. These filtering algorithms can predict future data based on the IMU's historical data and current data, thereby reducing the impact of random errors.
In addition to calibration and filtering algorithms, other technologies can also be used for IMU error compensation, such as data fusion technology. Data fusion technology fuses the output data of the IMU with other sensor data (such as GPS, wheel speed sensors, etc.), and uses the information from multiple sensors to correct the output data of the IMU to further improve the accuracy and reliability of the navigation and attitude measurement system. sex.
Summarize
To sum up, MEMS IMU error analysis and compensation are important means to improve the performance of navigation and attitude measurement systems. Through in-depth analysis and processing of systematic errors and random errors, the measurement accuracy of IMU can be significantly improved, providing more accurate and reliable navigation and attitude information for various application fields. ERICCO is a company specializing in the research and development of inertial navigation products. The independently developed MEMS IMU is deeply trusted by consumers across the country. MEMS IMU is light weight, small size, high performance, and can greatly save installation space, reduce carrier load, and reduce user expenses. Then the errors of such products can be adjusted at any time to minimize the errors. For example, the navigation level ER-MIMU-01 can autonomously seek north. The gyroscope that comes with the product is also relatively accurate. Compared with other inertial navigation companies, the error is still extremely small and the accuracy is slightly better.
If you want to know more about IMU, please contact our relevant technical personnel.
More Technical Questions
1.MEMS-IMU error calibration compensation method that does not rely on precision turntable
2.Application of Improved Wavelet De-noising Method in MEMS-IMU Signals
3.Research on error modulation technology of MEMS based on IMU rotation
4.Research on MEMS-IMU signal denoising technology
6.IMU self-calibration based on factorization
Products in Article
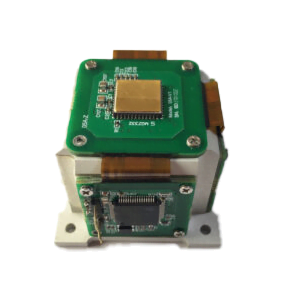
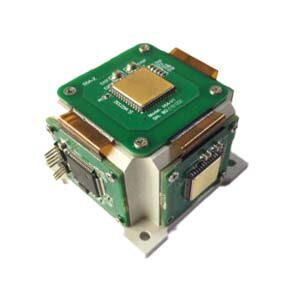
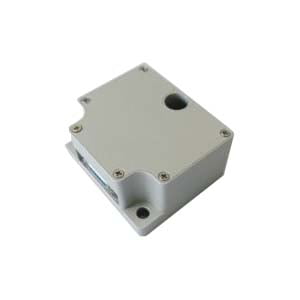
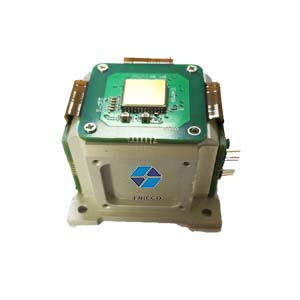
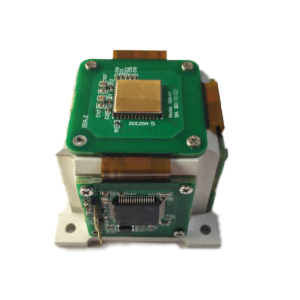
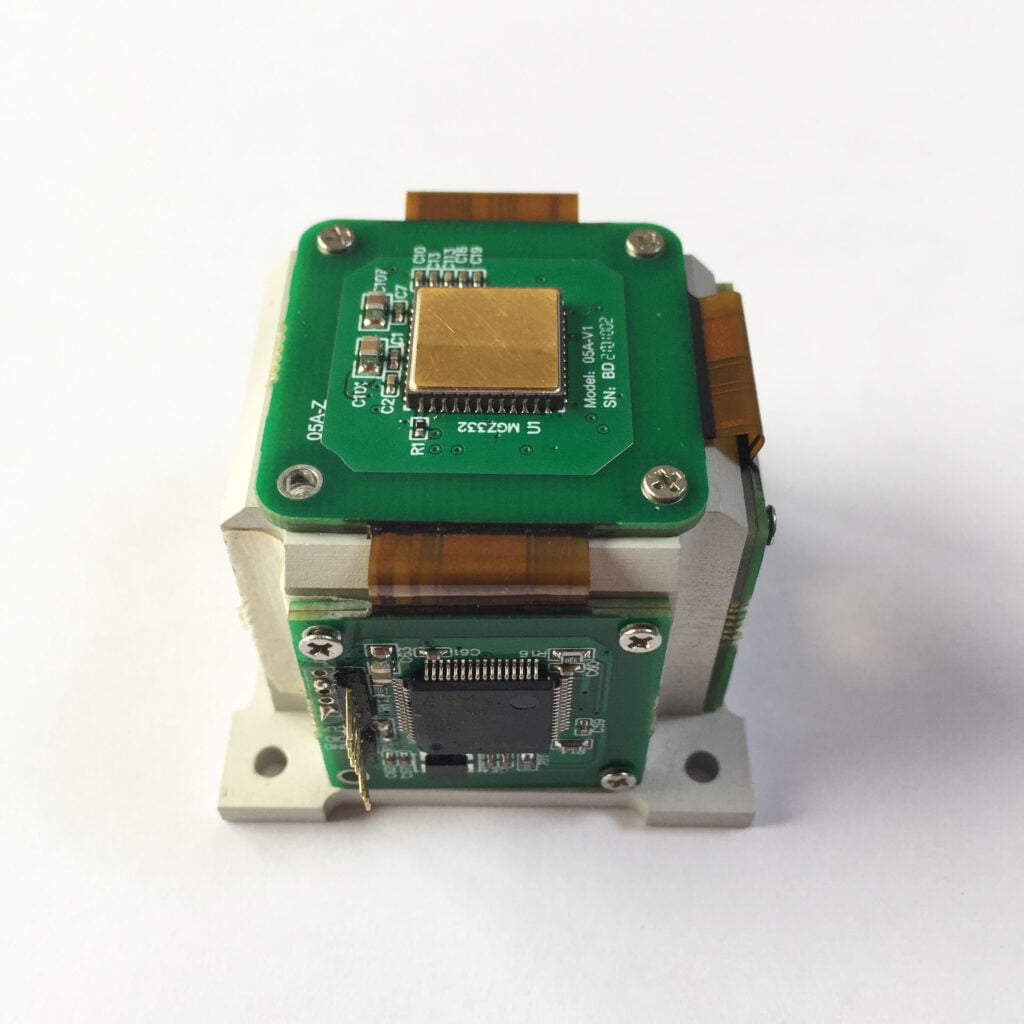