Quartz accelerometers, as one of the commonly used accelerometers, are mainly used to measure the acceleration of the carrier, it is a very important inertial device in the market.In the navigation and positioning of various carriers, the trajectory of the object can be obtained by measuring the acceleration, speed or position. However, because only the acceleration can be measured inside the moving object, the quartz accelerometer has a very important significance for inertial navigation technology.
The role of temperature coefficient
These core components are affected by temperature in practical applications, mainly in two aspects: first, the inertia device itself is sensitive to temperature, and the second is the device is affected by the surrounding temperature, that is, the temperature and the heat around the shell will cause errors within the device. The thermal expansion and cold contraction of the material will cause the deformation of the instrument structure parts, and the physical parameters of various internal materials will change accordingly, which directly affects the output stability, and then affects the navigation accuracy of the whole system. For this purpose, the ER-QA-03D can meet the normal operation in the operating temperature of -55℃ -180 ℃, and its offset repeatability reaches 50μg - 250μg, and the scale factor repeatability is 80 ppm - 250 ppm.
Temperature coefficient
Among the many indicators to measure the performance of quartz accelerometer, the stability of its offset value and scale factor are very important performance indicators, and also the prerequisite to ensure the high stability of quartz flexible accelerometer and even the high stability of inertial system. We know that the accuracy of inertial navigation system depends largely on the accuracy of inertial devices. The error of inertial navigation system is also formed by the accumulation of the error of inertial components in time, especially the inertial navigation system that needs to work continuously for a long time, the system error caused by the error of inertial components is astonishing.
Bias temperature coefficient
The offset value is the output value when the input acceleration of the quartz accelerometer is zero, and the change of the bias with temperature is called the offset temperature coefficient. The size and stability of the offset value is an important guarantee for the high linearity of the quartz accelerometer, especially when measuring small acceleration, the stability of the offset value is particularly important. The bias temperature coefficient of conventional accelerometers is about 30 ~ 100μg/℃. With the miniaturization of the inertial system and the requirement of low power consumption, the requirement of bias temperature coefficient is < 10 μg/℃ or even higher is put forward for the accelerometer. For example, the ER-QA-03A1 bias temperature coefficient can reach the range of < 10μg /℃, and the bias repeatability is ≤10μg and the scale factor repeatability is ≤15ppm. Based on the analysis and determination of the internal structure and properties of the material, the stability of the partial value affected by temperature is improved by the temperature compensating technology.
Scale factor temperature coefficient
The scale factor and its stability will directly affect the measuring accuracy of the accelerometer. Since the scale factor is determined by the common formula K1= = ml/Ktg, it is generally believed that ml (pendulum) and Ktg (torque coefficient of the torquer) are two factors that affect the change of the scale factor.It can be seen that the output scale factor is determined by the pendulum and the torque coefficient of the pendulum component. Because the quartz material is used, the thermal expansion coefficient is small, so the impact on the pendulum is small.In order to ensure the long-term repeatability of the scale factor of the quartz accelerometer, it is required to use high-performance permanent magnet materials. For the permanent magnet material used in the torquer, in fact, its stability largely depends on the stability of the magnetic system in various environments (including high temperature, low temperature, variable temperature, shock, overload, etc.). At present, the stability and repeatability of permanent magnet torquers and pendulum components are improved by screening more suitable permanent magnet materials combined with aging process.
From the above statement, it is not difficult to see the influence of temperature on the long-term stability of the quartz accelerometer. With the further study of the temperature coefficient of the offset value and scale factor, we can start from the relevant process technology to reduce the influence of temperature coefficient on the stability, so as to achieve the purpose of more accurate application of the quartz accelerometer.
More Technical Questions
1.What are the Advantages and Disadvantages of Quartz Accelerometers?
2.What is Sensitivity and Measurement Range in Quartz Accelerometer?
3.Quartz Accelerometer VS MEMS Accelerometer
4.What can you do with an Accelerometer?
5.Why do we Need Accelerometer?
6.What is the Purpose of the Accelerometer Senor?
Products in Article
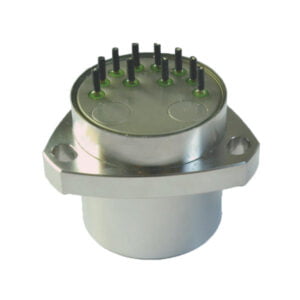
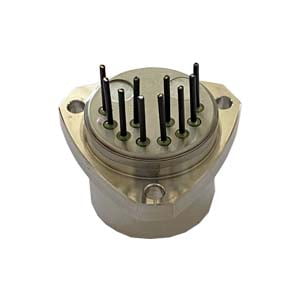
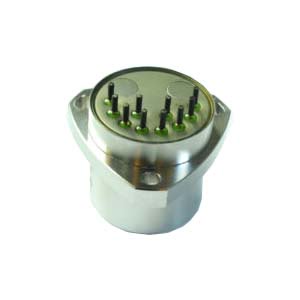
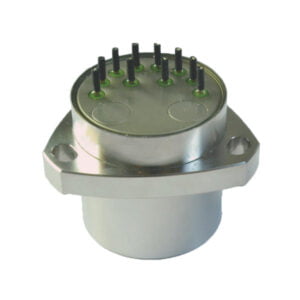
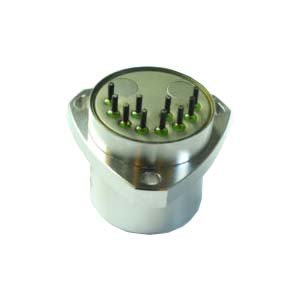
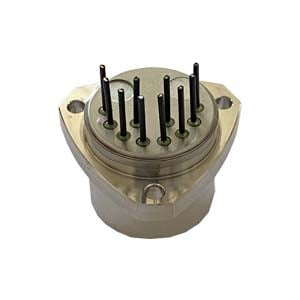