Different principle
MEMS gyroscope is the representative of the third generation of gyroscopes with the rise of micro-mechanical electronic systems (MEMS) and other disciplines, but also based on the Coriolis vibration effect and micro-nano processing technology.
The mechanical gyroscope is the representative of the first generation of gyroscopes, which works by using the gyroscopic effect, that is, the principle that the angular momentum of the rotating body remains constant in space.
Different structure
MEMS gyroscope sensor is usually composed of a MEMS gyro and a signal processor, MEMS gyroscope uses MEMS technology to manufacture a tiny vibration structure, by measuring the vibration frequency and vibration direction of the vibration structure to determine the rotation angular speed, no rotating parts, no bearings, has been proven to be mass production with micromachining technology, compared with mechanical gyroscope, its structure is simple, and it has become one of the most widely used gyroscope sensors. Known for its tiny 11 x 11 x 2 mm size, the ER-MG2-50/100 is designed for north finding, pointing, initial alignment/gyroscope tools, mining/drilling equipment, weapons/UAV launch systems, satellite antennas, target tracking systems, etc,in logging instruments. It also has bias instability of 0.01-0.02°/hr and angular random walk of 0.0025-0.005°/√hr, due to its high performance, The ER-MG2-50/100 can also be used for high-precision attitude measurement, stability control, positioning, navigation-grade MEMS IMU/ INS, land survey/land mobile mapping systems, railway train systems, etc.
Different from MEMS gyroscope, mechanical gyroscopes usually consist of a rotating rotor and a fixed bracket, and the rotation speed of the rotor is proportional to the external rotation angular speed, which is determined by measuring the rotation speed of the rotor. Its requirements for the process structure are relatively high, the cost is high, the structure is complex, and its accuracy is restricted by many aspects.
Different characteristics
MEMS gyroscope sensor has the advantages of high precision, fast response, small size, light weight and low power consumption. Compared with traditional mechanical gyroscopes, modern mems gyroscopes are more suitable for the large needs of the current market. Represented by the ER-MG2-300/400 high precision navigation MEMS gyroscope, with bias instability of 0.01°/ hour capable of measuring angular velocities up to ±400°/s, and has a digital output protocol compliant with SPI from mode 3. Angular rate data is expressed as 24-bit words. It features an advanced differential sensor design that eliminates the effects of linear acceleration, is capable of operating in extremely harsh environments where shock and vibration are present, and is sealed in a ceramic LCC surface mount package that effectively guarantees normal operation at 5V power supplies and a wide temperature range (−45°C to +85°C). Although the mechanical gyroscope sensor also has the advantages of high precision and fast response speed, it has been gradually replaced by other types of gyroscope sensors due to its complex structure, large volume, heavy weight, complex process and other shortcomings.
Different application fields
As a new MEMS gyroscope in modern production, it solves the shortcomings of large volume and mass and high cost of first-generation and second-generation gyroscopes, and with the continuous improvement of accuracy and stability, ER-MG2-50/100, ER-MG2-300/400 has the advantages of small size, low power consumption, low cost, strong anti-overload ability, large dynamic range, integrability, etc., which can be embedded in electronic, information and intelligent control systems, so that the system volume and cost are greatly reduced, and the overall performance is greatly improved. Therefore, it has a wide application prospect in the modern military field. High-precision micromechanical gyroscope will be used in missiles, aerospace, aircraft and other high-precision requirements of equipment, in addition, for modern emerging unmanned system navigation, satellite navigation positioning system, information mapping, resource exploration and other related fields have great application prospects. The mechanical gyroscope as the first generation product of the gyroscope due to the rapid increase in the demand of the modern market, the original process can not meet the needs, so the mechanical gyroscope gradually in the market gradually desalted.
If you are interested in MEMS gyroscope, please discuss with us.
More Technical Questions
1.Analysis of MEMS Gyroscope Drive Mode Control Loop
2.Basic Knowledge of Bias Stability of MEMS Gyroscope
3.How to select MEMS gyroscope?
4.What is the Hardware Interface of Ericco MEMS Gyro
5.Classification And Performance Improvement Of MEMS Gyroscope
6.Comparison Of Technical Specifications Of Navigation Grade MEMS Gyroscope
Products in Article
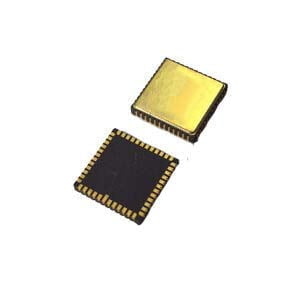
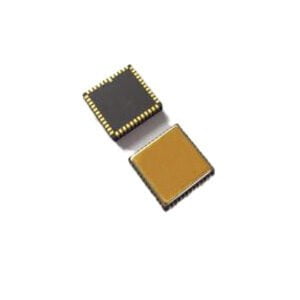
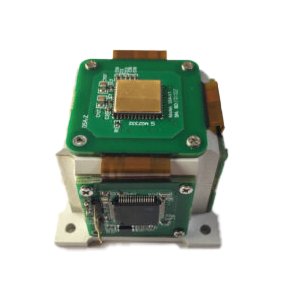
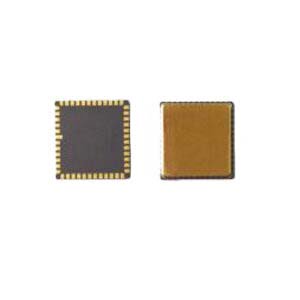
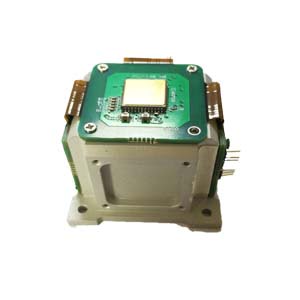
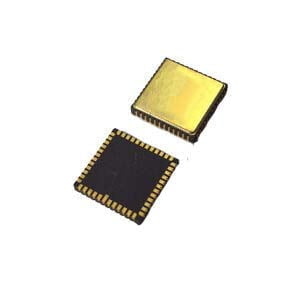