Construction surveying has long been a critical component in the intricate dance of planning, designing, and executing construction projects. Traditionally, the reliance on extensive control networks and optical instruments often led to delays and inefficiencies in survey operations. However, a transformative shift occurred with the advent of Global Navigation Satellite Systems (GNSS) in the 1980s, breathing new life into construction surveying and unleashing unprecedented energy in the sector.
- Background
The construction sector involves a variety of activities including design and construction of roads, buildings, rail, ports, bridges, and other major infrastructure. Site surveying is therefore essential for all construction projects as they provide fundamental information to support concept, design, construction, and subsequent project phases (e.g. control, monitoring, and as-built checks). Traditionally, site surveying was carried out based on extensive control networks and using optical instruments. These procedures were considerably slow and often caused a significant delay in a number of activities dependent on the timely release of survey data.
However, with the public deployment of GNSS systems in the 1980s, they were widely recognized and replaced traditional approaches, and were adopted in construction activities (e.g. setting out trenches, checking verticality of construction, measuring the dimensions of structural components). The employment of this technology has greatly improved the efficiency of survey operations, reduced errors‚ and improved the timeliness of survey data and its delivery to further stages of construction projects.
- GNSS in Site Surveying
While levels of adoption vary across construction activities, the influence and benefit of GNSS have been most noticed in infrastructure projects. GNSS systems have greatly improved different phases of these projects (including concept, design, construction, and maintenance), where reliable and repeatable centimeter-level accuracy is needed. Furthermore, improvements in GNSS technology and improved positional accuracy achieved using GNSS augmentation – specifically RTK GNSS with corrections delivered from the Ground-Bases Augmentation System (GBAS) network – have enabled easier collection and processing of spatial data and improved on-site productivity.
For example, in road construction, construction machines are used for levelling and adjusting the earth's surface. These modern construction machines use a 3D GNSS levelling system to achieve the projected shape and elevation of terrain with the required accuracy within permitted setting-out deviations according to the project. In the area of interest were realized geodetic check measurements. The aim was to objectively assess and evaluate the practical applicability of connection between a construction machine and precise surveying instrument for determination of position and height in real time.
3D GNSS levelling systems (Fig. 1) use highly resistant special angle sensors that are attached to the body of a construction machine. These sensors control the angles of individual work devices of machines. The system is able to calculate the precise position of the required work device of a construction machine according to measured angles and defined lengths. Thanks to the automatic control of hydraulics of construction machine, the share is adjusted to the desired tilt and height by itself according to the project. The system also allows the creation and storage of models with various tilts directly in the field. The 3D control unit processes signals from GNSS satellites, angle sensors and the reference station (or GPRS modem) and compares them with the stored designed values. One reference station can control any number of construction machines by using radio connection on the site. The altimetric accuracy of realized works ranges between 2 - 3 cm.
The combination of satellite and laser levelling system are used, representing a 3D GNSS levelling system with millimetre accuracy. This system allows determining heights with millimetre accuracy based on information about heights from the laser sensor located below the GNSS antenna. To standard set of GNSS reference station and moving receiver (rover), it is necessary to add the transmitter of the laser system and laser receiver to the antenna pole of a construction machine. The height difference with an accuracy of ±2.5 mm is calculated immediately. In applications of construction machines control, a millimetre accuracy for controlling the position of shear means huge savings in the material and the precise result of the work while maintaining all benefits from the use of GNSS.
Generally speaking, the major benefits of GNSS systems in site surveying applications can be summarized as:
- Time and efficiency improvements in surveying activities.
- Accuracy and repeatability of surveying procedure (specifically in risk management).
- Structured quality control through consistent and repeatable solutions.
- Reduced labor costs.
- Risk management in terms of accurate location of services.
- Ability to provide positional information instantaneously.
- Improved data exchange between different project phases (homogeneous data sets).
- Infrastructure savings (reduced requirement for survey ground control networks).
- Safety improvements through reductions in traffic management requirements.
3. GNSS Facilitate Construction Projects
In addition to site surveying, GNSS systems have facilitated construction projects by providing high-accuracy positional information (millimeter level) required for machine guidance, thus automating construction activities. Typically, machine guidance is used to automatically control the components of construction equipment (e.g. blades and buckets), where GNSS is integrated with inertial sensors to carry out precise positioning. These integrated positioning systems can be employed to provide different levels of machine interaction from indicative to fully autonomous.
In order to verify the productivity of GNSS-based machine control guidance in construction activities, Reykjavik University (Iceland) conducted a number of trench excavation studies on relatively small test sites using both traditional and GNSS-based machine-controlled techniques.
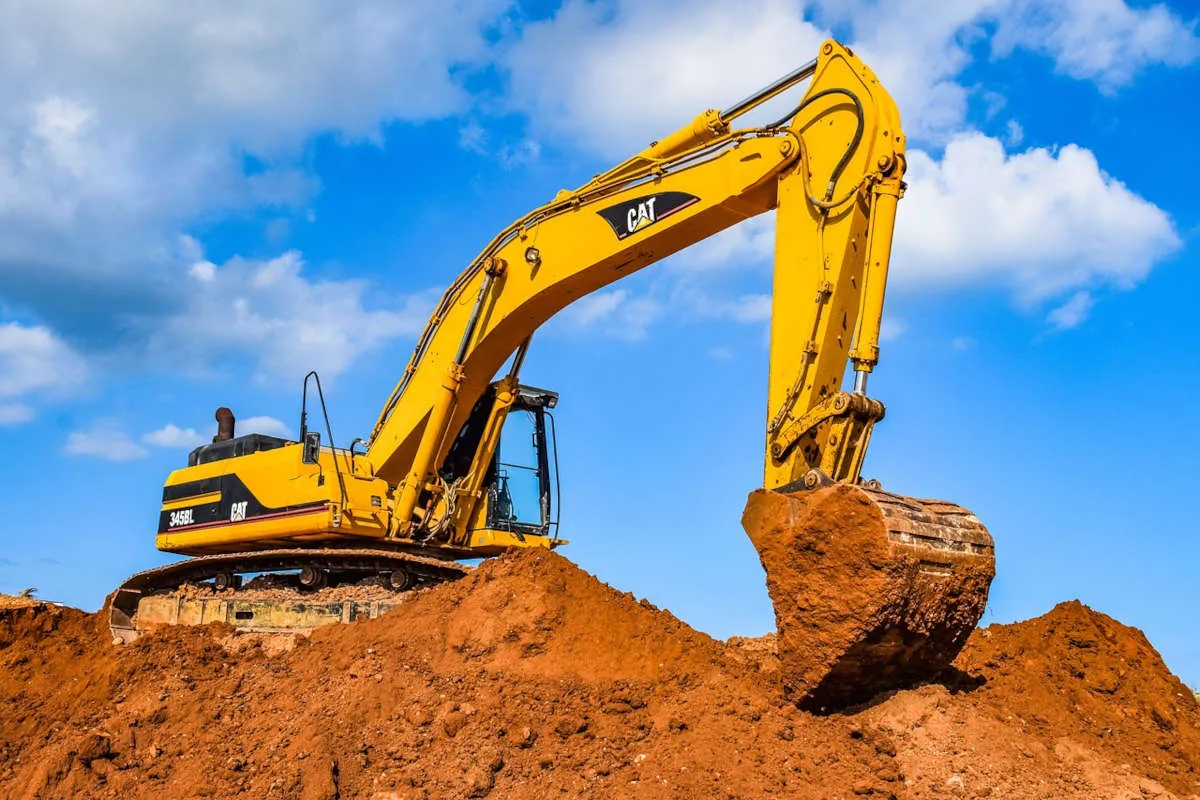
Figure 2 shows a Caterpillar 330DL hydraulic excavator equipped by GNSS receivers used in these comparative studies. Table 1 compares these two excavation approaches from the surveying time, accuracy, excavated material, and fuel consumption points of view and reports the productivity benefits of GNSS-based machine-controlled technique quantitatively.
Based on the comparison between traditional and GNSS-based machine-guided excavation techniques provided in Table 1, it can be concluded that using GNSS-based machine control techniques results in overall time and cost saving on construction projects.
The benefits of GNSS positioning techniques in machine guidance for construction activities can be consequently summarized as follows:
- Accuracy improvements – Execution of tasks in the first trial reduces operational inefficiencies, leads to fewer errors, and greater specification conformance.
- Reduction of potentially dangerous machine–worker interaction.
- Less machine depreciation.
- Fuel and capital savings.
- Maximized machine utilization and reduced downtime.
- Improved health and safety records.
With the growth and adoption of augmented GNSS-based machine guidance and its productivity and safety advantages, machine guidance is now increasingly being used in many construction projects. It is likely that this trend will continue, and machine guidance will be a standard requirement for construction-based projects.
4. Conclusion
In conclusion, the integration of GNSS technology into construction surveying signifies a revolutionary leap forward in the efficiency and accuracy of various construction activities. Traditional methods, relying on extensive control networks and optical instruments, have been outpaced significantly by the capabilities offered by GNSS systems. Integrated positioning systems enable varying levels of machine interaction, ranging from indicative to fully autonomous.
The deployment of GNSS in site surveying has not only streamlined operations but has also resulted in a notable reduction in errors and ensured the timely delivery of survey data throughout different phases of construction projects. Specifically, the ER-GNSS-B01 has been validated as a high-precision positioning directional board, supporting a comprehensive system with a full-frequency point on chip RTK positioning solution and a double antenna orientation solution. As a result, it proves to be a valuable asset in construction surveying, offering directional and precise positioning services.
Furthermore, comparative studies attest to the time and cost-effectiveness of GNSS-based machine control techniques, solidifying their integral role in modern construction practices. The accuracy improvements, mitigation of risks associated with machine-worker interactions, and overall productivity benefits highlight the transformative impact of GNSS in the construction industry. The increasing adoption of augmented GNSS-based machine guidance suggests that machine guidance will likely become a standard requirement for construction projects, further enhancing efficiency, safety, and overall project success.
In essence, the convergence of GNSS technology and construction activities heralds a new era of innovation and advancement in the field, promising unparalleled improvements in precision, efficiency, and project outcomes.
I will appreciate it if you find this article help you a lot, for more information, please read the following articles and products.
More Technical Questions
1. Performance Analysis of GNSS RTK Timing
2. Intelligent Urban Positioning: Using Multi-GNSS with 3D Mapping
3. Positioning Performance Comparison of GNSS PPP
4. Precision Mapping in Mining Operations: The Role of GNSS Augmentation Technology
5. Application of GNSS-RTK Positioning Technology in ICV Testing
6. Integration of GNSS Modules in Aviation: Precision Navigation for Unmanned Aerial Vehicles (UAVs)
Products in Article
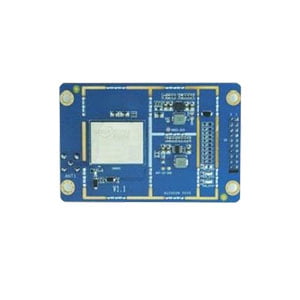
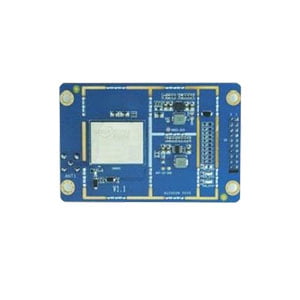
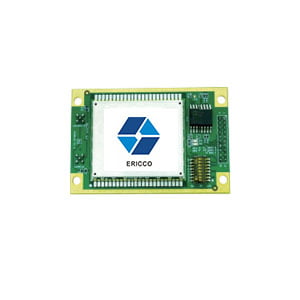
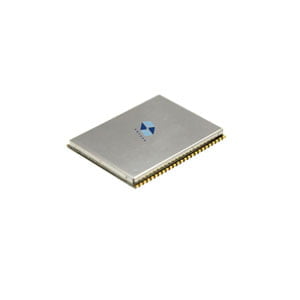
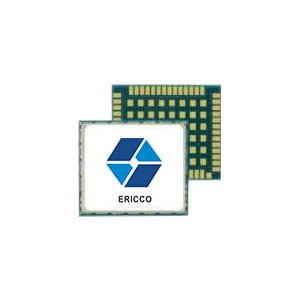
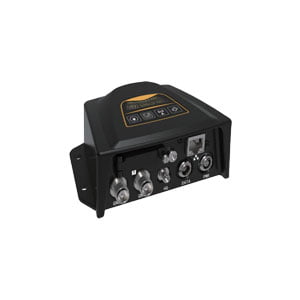