Fluxgate directional assembly is an important part of MWD, which is mainly composed of three-axis accelerometers and three-axis fluxgate sensor. It is mainly used in oil and gas, drilling, measurement while drilling, directional drilling and other fields, can measure well angle, tool face angle and azimuth angle. This article will introduce how fluxgate directional assembly play a role in MWD, and the following will introduce the concept of MWD, the components of MWD, and professional fluxgate directional assembly.
What is MWD?
MWD, which stands for measurement while drilling, is a system for taking measurements while drilling downhole, which allows measurements to be continuously sent to the surface while drilling. MWD uses gyroscopes, magnetometers, and accelerometers to determine downhole inclination and azimuth when drilling. Inclination is the angle of the hole with respect to the vertical direction, and azimuth is the angle of the hole with respect to the north. MWD uses mud pulses and electromagnetic telemetry to transmit the collected data to the surface. Once on the ground, the data is decoded and can then be sent to off-site locations. This allows engineers to make important decisions while drilling.
There are three important building blocks in MWD: IMU (Inertial Measurement Unit), the telemetry building block, and the ground system.
Inertial measurement is an important part of MWD. It is a general term for electronic devices that use sensors to calculate position and orientation. Almost all modern vehicles, from cars to airplanes, have some kind of IMUs. In the oil and gas sector, given that IMU is the "M" in "MWD," the industry sometimes refers to this building block simply as "MWD."
During a drilling operation, the machine operator responsible for manipulating the tool needs to know certain information about its current position in order to make informed decisions as it moves forward. Typically, this includes the current tilt angle of the well (hole) and the direction it is pointing in relative to the north. The building block of the MWD system responsible for making these measurements is the IMU located in the downhole. Once the measurement is made, the information needs to be encoded and sent to the ground - this is the telemetry building block. Finally, on the ground, the ground system is used to decode and display the information transmitted by the IMU.
Components of MWD
A complete set of MWD tools includes drill string, drill collar, MWD, mud motor, stabilizer and cutting bit. The MWD, mud motor, stabilizer and cutting bit are collectively known as the bottom hole assembly. Figure 1 shows the structure of the MWD tool, and the fluxgate directional assembly is an important part of the MWD. Figures 2 and 3 show the three-axis magnetometer and the three-axis accelerometers in MWD.
Figure 1 MWD structure
Figure 2 Three-axis magnetometer in MWD
Figure 3 Three-axis accelerometers in MWD
Fluxgate directional assembly
The fluxgate directional assembly, also known as the directional stub, is present in MWD tools, can resist vibration and shock, and can work in high temperature and harsh environments, including a three-axis accelerometer and a three-axis fluxgate sensor. ER-DOS-03 is a directional truncation for dynamic rotation measurement that uses a 24-bit high-resolution ADC to digitize the sensor's output signal for temperature drift and orthogonal compensation. The ER-DOS-03 accurately measures well angle, tool face angle and azimuth angle in the range of 0 to 150 ° C. It has built-in digital filters and compensation algorithms that can remove interference signals of vibration and rotation and accurately measure vibration and rotation at angles. Its digital output interface is UART or RS-232.
Advantages and features of ER-DOS-03:
Small size
Compact structure
Resistance to vibration and shock
High temperature resistance
Low power consumption
Rotational dynamic measurement is possible
High reliability
Conclusion
This paper starts with the concept and structure of MWD, expounds the relationship between MWD and fluxgate directional assembly, and introduces the working mode and existing characteristics of fluxgate directional assembly through a dynamic measurement orientation stub. Hopefully, this article has given you some insight into this knowledge.
If you are interested in this knowledge, please contact us.
More Technical Questions
1.GWD - Gyro-while-drilling Technology Superior to Traditional MWD
2.Three Signal Transmission Methods of MWD Inclinometer While Drilling
3.Development of MWD for Directional Drilling
4.What Is The Difference Between MWD And LWD?
5.What Is The Principle Of MWD?
6.How does MEMS gyroscope work in harsh high temperature environment?
Products in Article
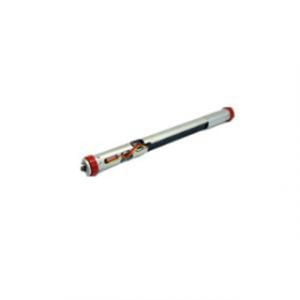
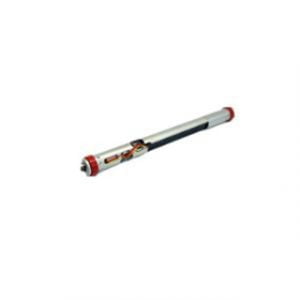
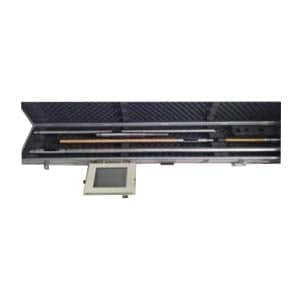
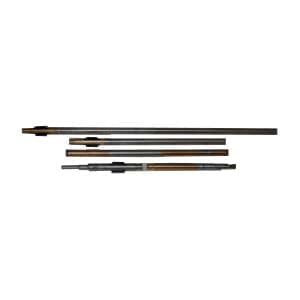
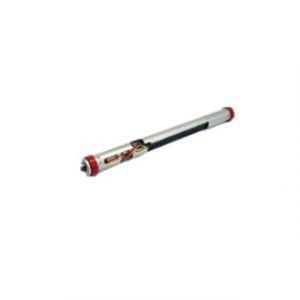
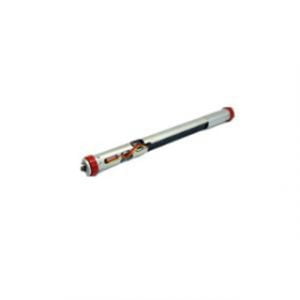